
RATS MRO Workshops
Thursday October 26, 2023

Introduction to Dry Gas Seals
Topic:
Introduction to Dry Gas Seals
Presenter(s):
Details:
Half-day (4-hour) interactive workshop
Exact time: 8:00AM to 12:00PM
Description:
The presentation aims to provide a comprehensive introduction to Dry Gas Seals, an advanced sealing component critical to the safe and reliable operation of high specification turbomachinery equipment.
Dry Gas Seals offer a robust, environmentally friendly sealing solution with minimal leakage of harmful emissions to the atmosphere, which is relevant more than ever in light of ever increasing emission focused legislations. The session presenter has worked within the turbomachinery industry for over 14 years at prominent rotating equipment providers. The session will delve into the fundamental principles associated with Dry Gas Seals and cover key topics such as:
• Design & Operation of Dry Gas Seals
• Wet Seal versus Dry Gas Seal Comparison
• Seal Support Systems
• Reliability & Failure Analysis
• Separation Seals
Attendees can expect an exploration of the advantages and challenges posed by DGS, along with real-world case studies highlighting successful applications. The presentation will cater to a diverse audience, including engineers, maintenance professionals, and industry stakeholders, offering valuable insights into optimizing performance, mitigating issues, and ensuring the reliable operation of centrifugal compressor systems employing Dry Gas Seals. This session promises to be an informative and engaging resource for those seeking a foundational understanding of an often misunderstood and highly engineered sealing product.
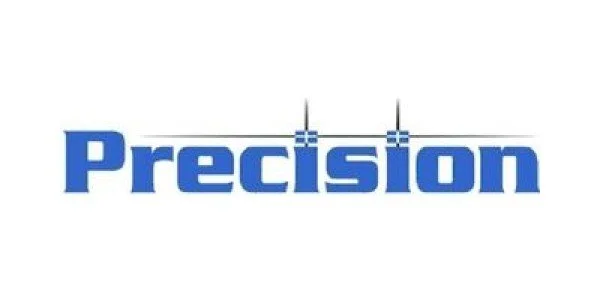
Compressors - The Practical Approach
Topic:
Compressors - The Practical Approach
Presenter(s):
Details:
Half-day (4-hour) interactive workshop
Exact time: 8:00AM to 12:00PM
Description:
"Compressors – The Practical Approach©" is an introductory course in the design, installation, troubleshooting and operation of compressors. A three day version of this course has previously been taught through the continuing education department at the Northern Alberta Institute of Technology, Edmonton, Alberta and for customers throughout Western Canada and the Middle East.

Intro to Reciprocating Compressors, Components, and Troubleshooting
Topic:
Intro to Reciprocating Compressors, Components, and Troubleshooting
Presenter(s):
-
John Ladd is the Engineering Manager at HOERBIGER Service Inc. based in Houston, TX. He supports the North America service branches providing repairs and upgrades on Reciprocating Compressors for the Oil & Gas and Chemical/Petrochemical industry. Prior to his current role he was a Solutions REE Engineering Specialist and Compressor Analyst at HOERBIGER Service Inc. John earned his Master's in mechanical engineering at Colorado State University with a focus on legacy integral pipeline compressors.
-
Technical Trainer | Machinery & Vibration Analyst
With 20 years of experience in the Machinery Reliability field, I specialize in reciprocating piston compressors, hyper compressors, and gearbox analysis and machine protection. In my current role, I deliver technical training seminars and hands-on sessions, sharing my expertise in centrifugal and reciprocating machinery analysis, motion amplification, thermography, and ultrasonic testing.
I am passionate about creating and delivering customer-facing and online training courses, covering all aspects of reciprocating compressors and analysis/monitoring technologies.
Details:
Half-day (4-hour) interactive workshop
Exact time: 8:00AM to 12:00PM
Description:
Reciprocating compressor are critical for the entire oil and gas infrastructure but they are some of the most misunderstood and overlooked pieces of equipment. This course is designed to introduce engineers, operations, and maintenance personnel to reciprocating compressors and their performance defining components, as well as the underlying theory for their operation. This course will also cover the most common issues encountered and provide the tools to identify and troubleshoot these concerns.
Upon course completion, the participants will have solid foundation in reciprocating compressors and the knowledge to troubleshoot the most common concerns encountered.

The Essentials of Vibration Analysis
Topic:
The Essentials of Vibration Analysis
Presenter(s):
Details:
Half-day (4-hour) interactive workshop
Exact time: 12:00PM to 5:00PM
Description:
Often vibration analysis uses the response of a machine to dynamic forces to determine condition and faults. This workshop will describe fundamental aspects of vibration, why it is measured, how it is measured, how it is used to evaluate machinery, why vibration analysis can be difficult to master, factors that complicate vibration analysis, and characteristics of specific machines such as centrifugal pumps and electric motors.
Examples of faults and solutions will be provided. Subjects such as structural resonance, BB3 pump cross-over acoustic resonance, vane-pass, cavitation, mechanical faults, off BEP (Best Efficiency Point) operation, ball bearings, electric motors, vertical pumps, finite element modeling, and fluid whirl/instability will be discussed. Solutions to problems including resonance resolution through structural changes or damping will also be presented.
Tools and techniques will be presented to optimize data collection; modal testing, motion amplification cameras, multi-channel analyzers, and ODS/Modal animations. Many years of experience, failures, and successes will be shared to help the analyst become more efficient and effective with practical vibration analysis. The strengths and weaknesses of vibration analysis will be discussed; vibration is one of many tools and sources of information needed to make a good analysis and conclusion regarding machinery faults and condition.

Resonance
Topic:
Resonance
Presenter(s):
-
Kyle has been the general manager of Hydro Reliability Services for 10 years, based in Colorado, where he is responsible for:
• Pump Improvement Engineering
• On site pump performance testing
• Principal Vibration Analysis resource for Hydro Globally
• Thermographic imagery
• Hydraulic and Mechanical troubleshooting
• Experimental Modal Analysis
• Operating Deflection Shape
• Structural Analysis
• Finite Element Analysis
• Motor current diagnostics
• Warranty Evaluation
• Sales and growth development of the business model
Prior to that, he was the Operations Manager at Hydro East in Philadelphia and has also gained experience at a few other well known pump manufacturers since 1999.
He has a Mechanical Engineering degree from the University of North Dakota and is a Level IV Vibration Analyst.
Details:
Half-day (4-hour) interactive workshop
Exact time: 1:00PM to 5:00PM
Description:
Resonance is a condition that is often misdiagnosed and commonly goes undiagnosed, resulting in persistent high amplitude vibration issues for long periods of time. Structural resonance typically results in highly directional vibration and increased amplitudes that can be difficult to resolve without the proper engineering approach.
In 2023, Kyle led the workshop through an in depth acoustic resonance condition, and exploration of what solutions could be implemented. Building on this topic, this years workshop will discuss new examples of resonance, and introduce cost implications associated not only with damaging vibration, but how operating strategies can compound lifecycle costs.
This presentation will focus on methods for diagnosing resonance and technology available to develop effective solutions without resorting to costly trial-and-error methods. Material presented will be supplemented by a case study where a complex resonance problem was addressed for an end user in the refining industry. A multi-stage charging pump was exceeding alert levels at both the inboard and outboard bearing locations, with vibration amplitudes greatest in the vertical direction and a clear correlation with the time of the day. The inboard bearing housing vibration was much more directional than the outboard bearing housing vibration. Investigation revealed that both structural resonance and acoustic resonance were being excited, with the structural resonance limited to the inboard bearing housing and the acoustic resonance affected by fluid temperature. Our review of this case study will include a brief overview of resonance, methodology for field testing and diagnosis, and solution development and implementation.

Casing Distortion
Topic:
Casing Distortion - Hidden Enemy of Rotating Machinery
Presenter(s):
-
Roman is a Senior Reliability Engineer with Easy-Laser and is visiting from his homeland of Sweden.
He is responsible providing technical support to customers within industrial rotating equipment maintenance and machinery installation, preventive maintenance, product functionality and measurement technology.
Details:
Half-day (4-hour) interactive workshop
Exact time: 1:00PM to 5:00PM
Description:
Overview of casing distortion in rotating machinery - Causes, Impact and Resolutions.
We will be exploring the topic in great depth, diving into the underlying causs, measurement techniques, and best practices to prevent casing distortion.

Diagnosing and Solving Structural Resonance Issues
Topic:
Diagnosing and Solving Structural Resonance Issues
Presenter(s):
-
Kyle has been the general manager of Hydro Reliability Services for 10 years, based in Colorado, where he is responsible for:
• Pump Improvement Engineering
• On site pump performance testing
• Principal Vibration Analysis resource for Hydro Globally
• Thermographic imagery
• Hydraulic and Mechanical troubleshooting
• Experimental Modal Analysis
• Operating Deflection Shape
• Structural Analysis
• Finite Element Analysis
• Motor current diagnostics
• Warranty Evaluation
• Sales and growth development of the business model
Prior to that, he was the Operations Manager at Hydro East in Philadelphia and has also gained experience at a few other well known pump manufacturers since 1999.
He has a Mechanical Engineering degree from the University of North Dakota and is a Level IV Vibration Analyst.
Details:
Half-day (4-hour) interactive workshop
Exact time: 1:00PM to 5:00PM
Description:
Structural resonance is a condition that is often misdiagnosed and commonly goes undiagnosed, resulting in persistent high amplitude vibration issues for long periods. Resonance typically results in highly directional vibration and increased amplitudes that can be difficult to resolve without the proper engineering approach.
This presentation will focus on methods for diagnosing resonance and technology available to develop effective solutions. Material presented will be supplemented by case studies where resonance was detected in the field, including the process for diagnosis of the offending resonant mode, the solution development process, and a comparison of operating conditions before and after solution implementation.
-
This case study is of resonance in a boiler feed pump application at a combined cycle plant. In this case, two boiler feed pumps were exhibiting high vibration at 4 x the operating speed of the equipment, which coincided with the vane pass frequency of the first stage impeller. Because of the directional nature of the vibration, resonance was suspected and impact testing performed while the equipment was operating. A resonant mode was confirmed at approximately -9% separation from the 1st stage vane pass, less than the minimum 15% separation recommended. After observing that all four feet of the pump were fully torqued and the thermal expansion gibs not installed, both thrust end feet were released to attempt to detune the installation. This increased the margin of separation, but the vibration levels were still slightly above the alarm level at 0.30 – 0.35 IPS 0-Peak overall.
To better understand the natural frequencies present below 800Hz and their associated mode shapes, an offline modal analysis was performed. This required installation of 18 triaxial accelerometers on the pump casing and bearings housings and use of a 3lb PCB modal hammer to impact the structure and provide excitation. The captured data was used to animate the structure. Several options were provided to the plant to bring the vibration into an acceptable range. The decision was made to implement a solution that did not require removal of the equipment from service- installation of two dynamic vibration absorbers (DVA). This solution effectively reduced the vibration from the original 1.0 IPS 0-Peak down to 0.11 IPS 0-Peak without removing the pump from the field.

Bearing Failure Modes & Analysis
Topic:
Bearing Failure Modes & Analysis
Presenter(s):
-
Territory Manager central and northern Alberta.
James completed a Bachelor of Science degree in 1999 from the University of Alberta and subsequently spent 19+ years in territory management and technical sales.
-
Chris Rempel provides bearing related equipment design and maintenance expertise to many of Canada’s resource-based industries. He started with NTN in 2002 with a background in material handling equipment design. Focusing on Petroleum, Mining and the Pulp and Paper industry, Chris is very familiar with applications in extreme operating conditions. Chris holds his bachelor’s of Applied Science in Mechanical Engineering from University of Saskatchewan.
-
James Hassan has a mining-mechanical engineering background with over 5 years of professional work experience in the bearings industry. His work has focused on developing technical solutions to problematic bearing applications within the Food Processing, Forestry, Aggregate, Mining, and Steel market segments. His areas of expertise include the evaluation of root cause bearing failure analysis, applications review, cost-effective methods for bearing lubrication, shaft and housing fits, and the development and application of bearing maintenance and installation training. James holds his bachelor’s of Applied Science in Mining Engineering from Queen’s University.
Details:
Half-day (4-hour) interactive workshop
Exact time: 1:00PM to 5:00PM
Description:
Introduction to Bearing Failure Analysis (approx. 1 hour) – NTN will present Bearing Failure Modes and Typical Causes. This presentation will cover topics including commonly observed bearing failure modes & causes, terminology, and visual appearance.
Failure Analysis Process (approx. 1 hour) – NTN will discuss the importance of bearing failure analysis as well as outline the process used to perform an effective analysis. This discussion will include steps throughout the analysis process including parts and data collection, observations & measurements, discovery meetings, technical reporting, and follow up.
Hands-on Bearing Failure Case Study Examples (approx. 1.5 hours) – NTN will provide multiple real-life samples of bearing failures for analysis. Attendees will split into groups of four to five people and visit each of the failure samples where they will use the theories, tools, and techniques discussed in the previous sessions to analyze the likely root cause of failure for each sample.
Bearing Failure Case Study Examples Review (approx. 0.5 hour) – NTN will review each case study failure sample with the attendees and compare findings between groups.

Importance of Machinery Installation
Topic:
Road Towards Reliability: Importance of Machinery Installation
Presenter(s):
-
Roman is a Senior Reliability Engineer with Easy-Laser and is visiting from his homeland of Sweden.
He is responsible providing technical support to customers within industrial rotating equipment maintenance and machinery installation, preventive maintenance, product functionality and measurement technology.
Details:
Half-day (4-hour) interactive workshop
Exact time: 8:00AM to 12:00PM
Description:
This is a very practical and demonstrative course on proper installation of rotating equipment and turbomachinery, such as pumps, compressors, turbines, and electric motors.

Pump and System Hydraulics for Reliability Engineers
Topic:
Pump and System Hydraulics for Reliability Engineers
Presenter(s):
-
Scott Shults is a Solutions Engineer for ITT/ Goulds Pumps. Scott has 16 years of experience in the pump industry and specializes in pump and system hydraulics as well as pump troubleshooting. He performs field testing throughout North America in power plants, refineries, chemical plants, etc. Scott has publications with the Turbomachinery & Pump Symposium and Hydraulic Institute and is a winner of the 2021 ITT Overall Award for a successful troubleshooting/cloud-based monitoring project at a pipeline.
Scott is a licensed professional engineer (P.E.). He holds a BS in mechanical engineering from Penn State University and an MS in mechanical engineering from Lehigh University.
Details:
Half-day (4-hour) interactive workshop
Exact time: 8:00AM to 12:00PM
Description:
This workshop is a continuation of the 1-hour presentation from Oct. 25, 2023. The workshop addresses the fundamentals of pump and system hydraulics. This includes how to read a pump curve, what the best efficiency point means, and what the two major types of cavitation are. It addresses the myriad difficulties of running pumps in parallel and includes a heavy dose of field issues. Participants will learn how to develop a system curve and the influence of the system curve on pump reliability.
This workshop applies to you if:
You have poor pump bearing and seal reliability
You break pump shafts
You operate dissimilar pumps in parallel
You need more flow in your system
You don’t understand how the system curve interacts with the pump curve
Your pump has high vibration
Your pump sounds like it’s pumping gravel
You’re considering using a VFD
You’re responsible for pump reliability

Mechanical Seal Basics & Seal Support Systems
Topic:
Mechanical Seal Basics & Seal Support Systems
Presenter(s):
-
Ananth Kumar is Chief Engineer for John Crane Canada. He has a total of 43 years of pump and seal experience, having been involved in design, commissioning, trouble shooting and training. He has worked with Pump and Seal manufacturers around the world and has been with the Engineering group in John Crane Canada for the past 23 years. Ananth has a Master’s degree in Mechanical Engineering and is a registered Professional Engineer in the Province of Ontario.
Details:
Full-day (8-hour) interactive workshop
Exact time: 8:00AM to 5:00PM
Description:
This training course is intended to meet the learning needs of End User, OEM & Contractor personnel working with rotating equipment, such as centrifugal pumps used in the process industries. The course will focus on basic and advanced concepts with the aim of providing attendees with a working knowledge of Mechanical Seal Basics (Morning) and Sealing Support Systems (Afternoon).
Key objectives of the course include:
Understand the fundamental principles of mechanical seals and support systems used in rotating equipment
Overview of mechanical seal engineering principles
When would you select a single seal, dual unpressurized seal, dual pressurized seal, a seal with a ‘back-up’ containment seal and what are the appropriate piping plans for each.
Solving mechanical seal reliability issues where miss-selection of seals and/or seal system piping plans could have or did result in unreliable or troublesome operation.
Conduct a detailed observation analysis to identify and resolve mechanical seal failures associated with rotating equipment
API Piping plan overviews and best practices for the most common types of mechanical seal support systems
Understand and be able to apply the latest sealing technology used on process applications
Be able to adopt safe working practices at all times when working with mechanical seals and support systems
Understand the importance of mechanical seal performance for overall process plant reliability

Fluid Film Bearings for Heavy Air Handlers
Topic:
Fluid Film Bearings for Heavy Air Handlers
Presenter(s):
-
Received his Bachelor of Science in mechanical engineering from York College of Pennsylvania. He has spent 4 years with Dodge Industrial as an application engineer for hydrodynamic bearings. His expertise includes: selecting bearings for new applications, assisting customers with technical questions, and creating and disseminating technical information.
-
Received his Bachelor of Science in mechanical engineering from Clemson University and an MBA from Western Governors University. He has spent 8 years with Dodge Industrial as a Field Sales Engineer and product manager for Plain Bearings.
-
Master Mechanical engineering Villanova University, Masters Industrial Engineering from Penn State University, LSME P.E., Over 25 years of experience with Dodge Industrial. (will be conferencing in from Greenville, SC).
Details:
Half-day (4-hour) interactive workshop
Exact time: 1:00PM to 5:00PM
Description:
This hands-on workshop will de-mystify fluid film bearings commonly used on large industrial blowers by explaining maintenance, operational, and condition monitoring best practices. The training will assume no prior knowledge on hydrodynamic bearings, but by the end you will be equipped to resolve problems on bearings that are often highly critical and highly obscure.
Discussion will include: Fundamental theory of fluid film bearings, common failure modes & remedies, comparison between rolling element bearings and journal bearings, bearing rework: pros & cons, and benefits of circulating oil.

Machinery Installation & 5-Step Alignment Fundamentals
Topic:
Machinery Installation & 5-Step Alignment Fundamentals
Presenter(s):
-
John-Paul manages Benchmark PDM’s every day activities including the service and rental department, with a focus on providing sales and support to the sales network across Canada for Easy-Laser alignment & measurement systems. He assists in training mechanics, millwrights, tradespeople and laser alignment end-users on how to perform the correct measurements when dealing with rotating machinery. He also goes out into the field to help companies in all types of industries to align their machines with precision alignment technology saving them time and money.
Details:
Half-day (4-hour) interactive workshop
Exact time: 1:00PM to 5:00PM
Description:
This workshop will cover the detection and removal of what we call the roadblocks to achieving correct installation or re-installation of a machine. This is mainly the removal of machine stress with a focus on flatness or level of a machine base and of course, the biggest roadblock of all – misalignment. Using laser alignment and measurement equipment, we go through the applicable measurement programs, where to use them and why. We also run through important and realistic situations that prevent proper shaft alignment like navigating around bolt bound and base bound issues or thermal machine growth.
This workshop will use the ANSI Shaft Alignment Methodology as a guideline as well as cover the required elements of the new Canadian Machinery Vibration Association (CMVA) shaft alignment certification program.

Pump and System Hydraulics for Reliability Engineers
Topic:
Pump and System Hydraulics for Reliability Engineers
Presenter(s):
-
Scott Shults is a solutions engineer for ITT/Goulds. Scott has 15 years of experience in the pump industry and specializes in pump and system hydraulics as well as pump troubleshooting. He performs field testing throughout North America in power plants, refineries, chemical plants, etc. Scott has publications with the Turbomachinery & Pump Symposium and Hydraulic Institute and is a winner of the 2021 ITT Overall Award for a successful troubleshooting/cloud-based monitoring project at a pipeline.
Scott is a licensed professional engineer (P.E.). He holds a BS in mechanical engineering from Penn State University and an MS in mechanical engineering from Lehigh University.
Details:
Half-day (4-hour) interactive workshop
Exact time: 1:00PM to 5:00PM
Description:
This workshop addresses the fundamentals of pump and system hydraulics and is not only for Reliability Engineers. This includes how to read a pump curve, what the best efficiency point means, and what the two major types of cavitation are. It addresses the myriad difficulties of running pumps in parallel and includes a heavy dose of field issues.
This workshop applies to you if:
You have poor pump bearing and seal reliability
You break pump shafts
You operate dissimilar pumps in parallel
You don’t understand how the system curve interacts with the pump curve
Your pump has high vibration
Your pump sounds like it’s pumping gravel
You’re considering using a VFD

The Full Lifecycle of an Industrial Gear Reducer
Topic:
The Full Lifecycle of an Industrial Gear Reducer
Presenter(s):
-
Dan is the General Manager of the Applied Edmonton Shop and has extensive experience repairing and troubleshooting gear products. Initially starting as a Repair Coordinator in the shop he has seen thousands of gear reducers of all makes and model come through the facility to be repaired. Over the years he has participated in analyzing reducer failures and proposing upgrades for countless customers over a broad mix of industrial applications. Dan is an expert on helping to improve the service life of gear reducers by knowing what makes them fail and working to help preventing those failures from reoccurring. Dan has over 15 years of experience through all industries, including but not limited to oil and gas, mining and forestry.
-
Glenn is a Senior Application Specialist with Applied’s Technical Solution Team, with over 25 years of service/experience. From growing up on the family farm to our customer’s site, Glenn has a talent for working with mechanical equipment. When talking to Glenn, one really gets a sense of the enthusiasm and passion he has working with his customers. Glenn provides solutions while troubleshooting for customers mechanical issues through implementation of design changes that help improve equipment service life, increase performance, reliability and reduce maintenance costs provides a trues sense of satisfaction. The results of which can be appreciated for years to come.
Details:
Half-day (4-hour) interactive workshop
Exact time: 8:00AM to 12:00PM
Description:
This workshop will help participants further understand gear reducers by joining members of the Applied team while they walk them through the complete life cycle of a gearbox. The team will present using real world examples including practical exercises that directly correlate to the presented material of what participants will see out in industry.
The team will start at the beginning of the service life of a gear reducer, with an outline of the selection process that occurs when a new application arises through either facility expansion or upgrade. The presenters will work through all the critical information that is required to properly select the size, type, and purpose of a gearbox to ensure the best piece of equipment for long term success/ application. The workshop will provide opportunity for hands on interaction through disassembly of an industrial gearbox to discussion of the internal workings of the gear train on top of different versions of speed reducers used in industry, including one particular design that uses no gears at all (SM Cyclo).
Next the workshop will move on to the components around the gearbox, from selecting couplings and breathers to the proper cooling and lubrication required for successful operating function. The workshop will highlight additional non-traditional aspects for the needs beyond just the gearbox itself.
Next, the workshop will review best practices should be followed while the unit is in service to reduce downtime, prolong the life of the unit and ensure it provides the desired results. The workshop will also review repair processes and what upgrades can be completed once a unit is already in service to address any maintenance issues that arise safeguarding the operations and expanding the life of the equipment.
Finally, the workshop will conclude with an outline what options are present as the unit reaches the end of its service life as it either becomes obsolete or the needs of increasing production requirements grow.

Sustainable approach to Turbine Lubricant Maintenance
Topic:
The Three R’s: A Sustainable Approach to Turbine Lubricant Maintenance
Presenter(s):
-
Matthew G. Hobbs is an accomplished young scientist and avid mountaineer who firmly believes that career success is similar to success in the mountains. Both start with a vision which requires planning, training and cooperation amongst teammates to achieve. The ascent then depends upon hard work, route-finding, overcoming obstacles, the ability to manage risk and unfailing dedication to one’s goal. On the summit, the reward for these sacrifices is unparalleled.
Details:
Half-day (4-hour) interactive workshop
Exact time: 8:00AM to 12:00PM
Description:
Sustainability and maintenance go hand-in-hand. By definition, something must be maintained for it to be sustained. To ensure sustainable power generation, effective turbine lubricant maintenance is, therefore, imperative. Despite its recognized importance, existing oil maintenance programs are often reactive instead of proactive in scope. Indeed, most maintenance programs target physical contamination without addressing the underlying chemical causes of costly oil-related failures. This approach, inherently, treats turbine oils as consumables. For power generation to move towards true sustainability, however, lubricants need to be regarded as assets to be proactively cared for rather than reactively replaced.
During the 1980s, early sustainability programs highlighted the value of “The Three Rs” (Reduce, Reuse, Recycle). A different set of Rs will prove similarly effective with respect to making turbine oil maintenance more sustainable: Rethink; Remove; Restore. By building on these pillars of effective lubricant maintenance, turbine operators can make meaningful contributions towards sustainability in power generation.

Intro to Reciprocating Compressors, Components, and Emissions
Topic:
Intro to Reciprocating Compressors, Components, and Emissions
Presenter(s):
-
John Ladd is the Engineering Manager at HOERBIGER Service Inc. based in Houston, TX. He supports the North America service branches providing repairs and upgrades on Reciprocating Compressors for the Oil & Gas and Chemical/Petrochemical industry. Prior to his current role he was a Solutions REE Engineering Specialist and Compressor Analyst at HOERBIGER Service Inc. John earned his Master's in mechanical engineering at Colorado State University with a focus on legacy integral pipeline compressors.
-
Klemens Kuderer is the Global Engineering Expert at HOERBIGER Vienna GmbH based in Austria. He supports the regional engineering departments providing simulations and advanced studies on Reciprocating Compressors for the Oil & Gas and Chemical/Petrochemical industry. Prior to his current role he was Product Manager Mechatronics in Singapore for Asia/Pacific and Global REE Auditor. Klemens earned his Master’s in international industrial engineering at University of Applied Science at Technikum Vienna.
Details:
Half-day (4-hour) interactive workshop
Exact time: 8:00AM to 12:00PM
Description:
Reciprocating compressor are critical for the entire oil and gas infrastructure but they are some of the most misunderstood and overlooked pieces of equipment. This course is designed to introduce engineers, operations, and maintenance personnel to reciprocating compressors and their performance defining components, as well as the underlying theory for their operation. This course will also review the sources of emissions and provide the end users a road map on how to mitigate these concerns.
Agenda:
Introduction to Reciprocating Compressors
How do they work
What are the major components
Introduce the API 618 Data Sheet
Theory of Compression
Introduce the governing equations
Compressor capacity control methods
Understand how losses effect the compression process
Introduction to Compressor Valves
How do they work
Review the different types
Performance defining characteristics
Introduction to Rings and Packing and Emissions Mitigation
How do they work
Design considerations
Means to optimize performance