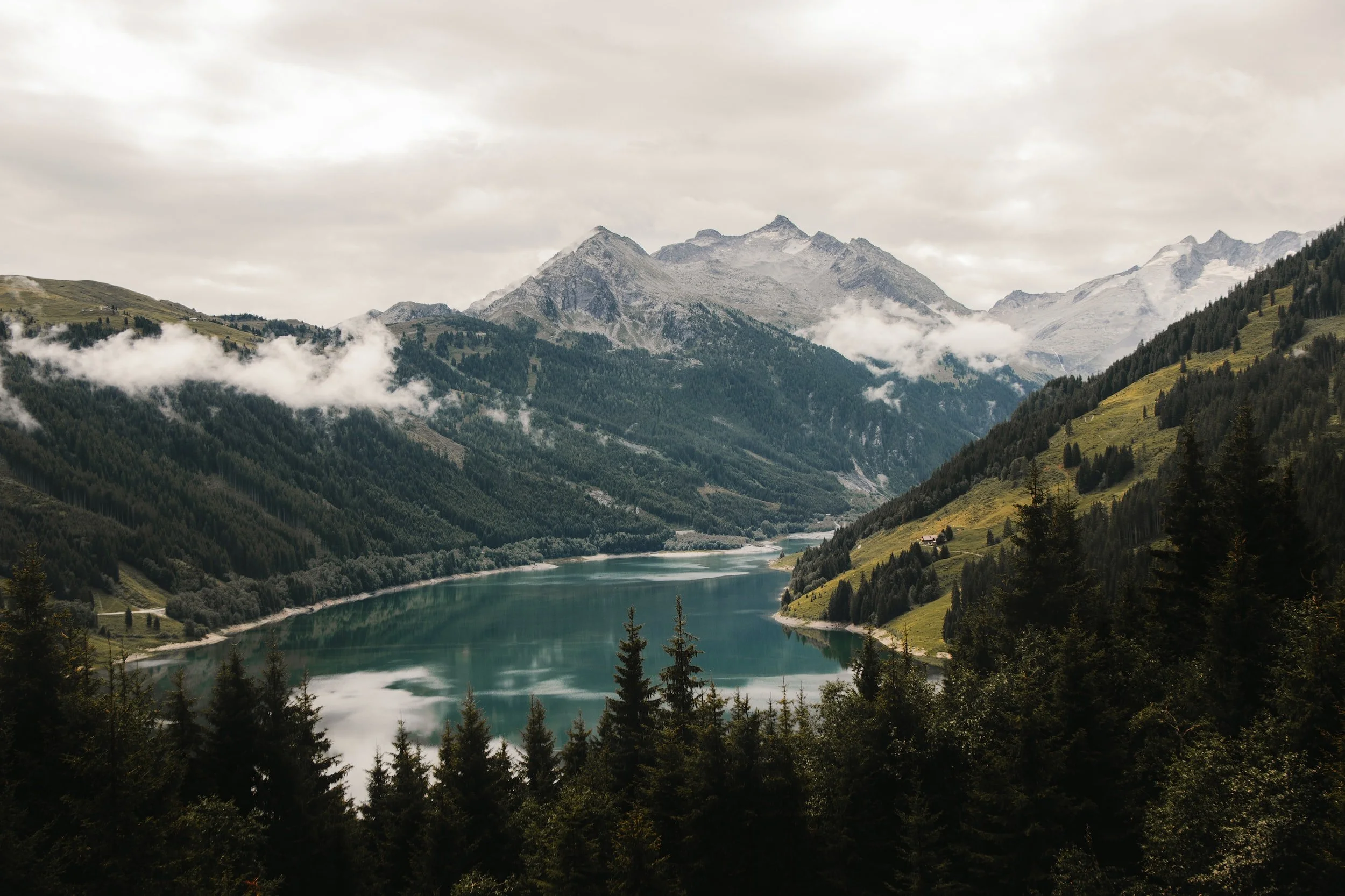
RATS MRO Conference
Presentation ARchive
2023 Presentations
2022 Presentations
2018 Presentations

Reducing Emissions in Reciprocating Compressors through Engineered Revamps
TOPIC:
Reducing Emissions in Reciprocating Compressors through Engineered Revamps
INSTRUCTOR(S):
-
As Director of Technical Solutions, Craig leads a highly skilled team of technical professionals focusing on solving complex issues and maximizing the peak performance of reciprocating compressor systems. This includes revamp projects, technical support, troubleshooting activities and investigations, reverse engineering, and many other miscellaneous compressor related projects. Craig has over 16 years of reciprocating compression experience with Burckhardt Compression having worked in a variety of roles with the company supporting end user equipment across the globe. Craig is a Millwright by trade having graduated from Durham college with continued learnings through field experience and reciprocating compressor related training courses.
DETAILS:
One (1) hour presentation, including up to 15 min. Q&A
DESCRIPTION:
There is no doubt that the push to reduce emissions across the globe and specifically in Canada will only be picking up steam in the years to come given the ambitious goals set out by governments around the world. The 2030 Emissions Reduction Plan set forth outlines a sector-by-sector path for Canada to help do our part by reaching the country's emissions reduction target of 40 percent below 2005 levels by 2030 and net-zero emissions by 2050. As members of the Energy / industrial community there is an immense amount of responsibility on end users and equipment suppliers to help aggressively drive down the emissions that are produced through operating equipment at the various facilities across Canada.
There are increasingly more local penalties and fines for flaring that are now being enforced so end users have no choice but to adapt with new designs to re-route the previously vented gas to an appropriate containment. One of the ways in which emissions can be reduced for reciprocating compressors is through engineered revamps solutions. This presentation will cover some of the different ways in which these new designs can help reduce leakage rates and improve the overall efficiencies of compressors. This can be done by upgrading packing materials, design changes to the packing case and sweep/purge/buffer systems, with the option to reinject leak gas back into the compressor system.
Throughout this presentation we will explore some of the different examples of compressor applications that would benefit from utilizing sealing system and recovery system revamps to lower and ultimately eliminate emissions.
Properly executed these revamps will result in improved process efficiencies, reduced operational expenses, reduced environmental impact, where possible increase mean time between outages and of course contribute to a healthier social license.
Burckhardt's approach to reducing emissions from reciprocating compressors can be adapted in a multistep approach.
Step 1. Compressor health survey. Perform a comprehensive compressor system assessment that helps you get a baseline of your compressors systems condition. It should include:
An assessment of previous maintenance and operational history
Recommendations for activities that can improve compressor performance
A full report of the health of your system for your records
Step 2. Packing system upgrades: Design a custom sealing solutions (Packing and Piston) for your compressor based on its current operating conditions. This packing case will use a series of different elements to allow for increased sealing efficiency and meantime between overhauls.
Step 3. In addition to the sealing system upgrades, monitoring can be added for better predictive maintenance. This would typically be temperature and flow monitoring of the leak gas along with buffer and purge panels. The additional monitoring and buffering will allow operations and maintenance to make predictive decisions on interventions. This will eliminate the need to use time based maintenance and ultimately decrease operational expenses.
Step 4. If conditions are adaptable, the leak gas can be reinjected back into the suction gas stream or other locations of the plant. This is the full circle of emissions reduction. Depending on application there could be a booster compressor installed to take the leak gas which would typically be sent to safe location or flare and reinject it into a useful stream of the system. This not only saves from gas being lost to the environment but it keeps the gas where it can continue to create value for your compressor system.
Efficiencies do not stop at just the sealing systems. Additional efficiencies can be found in converting lubricated compression systems to dry running. This reduces the operational expense for cylinder lubrication, maintenance on lubricators, maintenance on filtration, and downstream equipment.
Compressor valves can also be assessed for efficiencies, using the latest technology compressor valves can create increased flow and reduced energy consumption.
Using a combination of approaches to compressor emissions reduction, you can greatly increase the efficiencies of your compressor systems and reduce their operating costs.
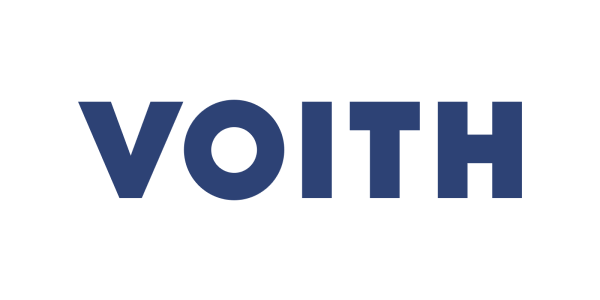
Starting Methods for Large Electrical Motors on Turbomachinery Packages
TOPIC:
Starting Methods for Large Electrical Motors on Turbomachinery Packages
INSTRUCTOR(S):
-
Brandon Moy has 12 years experience in industrial drive trains and has supported a broad range of applications from conveyors, crushers to compressors and pumps. He currently provides drive train solutions specializing in hydrodynamic drives.
Brandon received his Bachelors in Applied Sciences, Mechanical Engineering from the University of Waterloo.
-
Helmut has been with Voith Turbo in Crailsheim / Germany for over 41 years, of which he spent 34 years in the Variable Speed Drives and Industry Service. In his current position as Service Business Development Manager he is working for the Industry Service business line.
Helmut started in Service at Business Unit (BU) Variable Speed Drives in 1989 covering all areas in Customer Service and progressed to Field Service and Repair Management in 1993. Between 2001 and 2007 he was heading the Field Service, Competence Center Vorecon Service and the Service Workshop at BU Variable Speed Drives in Industry Division. From 2007 to 2016, he was General Manager Technical Sales After Market Business at BU Variable Speed Drives, Division Power, Oil & Gas.
Helmut has extensive experience in all areas of the Variable Speed Drives and Industry Service and has worked in various leadership positions at Voith Turbo. His strong customer focus and ability to coordinate complex processes makes him a valued partner to our customers.
DETAILS:
One (1) hour presentation, including up to 15 min. Q&A
DESCRIPTION:
Electric Motor Drives in the power range from 1,000 to 60,000 HP are often used for turbomachinery applications. The electric drive systems used include electric motors with variable frequency drives (VFD), electric motors with variable speed planetary gear hydraulic drives (VSHD), and constant speed electric motors.
Two issues tend to require discussion, and a significant level of expertise to avoid problems:
First, the startup has to be accomplished without exceeding the maximum permissible voltage dip limits at the point of common coupling (PCC). In case of strong supply networks, a direct online start-up usually works. However, safe start-up solutions are also available for weak supply networks by using common starting devices. Torsional transients during the starting process have to be considered.
Therefore, this tutorial presents a rough overview of proven start-up methods for direct online operating electric motor drives. Pros and cons are discussed. Based on a starting by means of a pony-motor, which is connected to a hydrodynamic variable speed planetary gear, the run-up process is discussed in detail. It can be seen that the grid disturbances are negligible especially for synchronous main motors.
Second, the choice of drive impacts the train’s torsional characteristics, shaft endurance limits and operational flexibility. Torsional integrity of the electric motor driven trains are critical to safe and reliable operation, and must be considered during the design, selection and packaging of the train’s key components (motor, gearbox, couplings and the compressors).
This tutorial outlines a methodology used to ensure torsional integrity in standardized Electric-motor-driven gas compressor packages. In addition to steady-state torsional analysis, the drive harmonics from electrical sources (steady-state pulsation) and the drive’s characteristics at fault-events such as phase-to-phase faults (transients) are incorporated into the torsional model to perform a complete torsional analysis. Shaft stresses are evaluated over a wide range of motor frame sizes, and consequently couplings and gearboxes. Couplings and gearboxes are designed to handle the mean torque and peak transient torques as appropriate.

Pump and System Hydraulics for Reliability Engineers
TOPIC:
Pump and System Hydraulics for Reliability Engineers
INSTRUCTOR(S):
-
Scott Shults is a solutions engineer for ITT Goulds Pumps. Scott has 16 years of experience in the pump industry and specializes in pump and system hydraulics as well as pump troubleshooting. He performs field testing throughout North America in power plants, refineries, chemical plants, etc. Scott has publications with the Turbomachinery & Pump Symposium and Hydraulic Institute and is a winner of the 2021 ITT Overall Award for a successful troubleshooting/cloud-based monitoring project at a pipeline.
Scott is a licensed professional engineer (P.E.). He holds a BS in mechanical engineering from Penn State University and an MS in mechanical engineering from Lehigh University.
DETAILS:
One (1) hour presentation, including up to 15 min. Q&A
DESCRIPTION:
This presentation addresses the fundamentals of pump and system hydraulics. This includes how to read a pump curve, what the best efficiency point means, and major causes of pump reliability problems. Participants will learn how to develop a system curve and the influence of the system curve on pump reliability.
This workshop applies to you if:
You have poor pump bearing and seal reliability
You break pump shafts
You need more flow in your system
You don’t understand how the system curve interacts with the pump curve
Your pump has high vibration
Your pump sounds like it’s pumping gravel
You’re responsible for pump reliability

VOC Legislation and LDAR Impacts on Ageing Pump Fleets
TOPIC:
VOC Legislation and LDAR Impacts on Ageing Pump Fleets
INSTRUCTOR(S):
-
Richard Smith trained as design engineer with the Ford Motor Company working in both production and product development.
For the last 38 years Richard’s has focused on sealing technology. Joining AESSEAL in 1989, Richard has worked within the application engineering of sealing technology.
Richard became a Director of AESSEAL in 1998 and for the past 19 years has been at the company’s forefront of the Oil Gas and Petrochemical Industry sectors being involved with the development of products for both upstream and downstream applications. Richard is currently AESSEAL’s representative on the API 682 Task Force.
Richard has had many papers published at international rotating machinery events and numerous articles published in international journals. These have mainly been on the practical application of mechanical seal technology in Industry.
DETAILS:
One (1) hour presentation, including up to 15 min. Q&A
DESCRIPTION:
Regulatory requirement for VOC reduction has been in force in the USA for several decades. In Canada best in class users have voluntarily adopted similar practices.
From January 2023 facilities that produces liquid petroleum products by means of distillation of hydrocarbon compounds and associated petrochemical plants will now be subject to Canadian regulations. This now mandates Leakage detection and repair (LDAR) testing of equipment components three times per calendar year. The regulations provide LDAR exemptions for certain configurations of pump dual mechanical sealing systems, however the regulatory wording is ambiguous.
The presentation will review the impact that the regulations will have on pump fleets reliability particularly operators with older fleets of pumps. The LDAR exemption options will be discussed along with some of the challenges of the Canadian climate. A proposed improved wording that is aligned with terminology used in international standards such as API 682 & trade bodies such as the Hydraulic Institute will be offered.
Case studies form both USA and Europe will be presented, for individual applications where technology has been applied to legacy pump machinery with minimal intervention. Case studies of large fleets of legacy pump machinery have been upgraded to dual seals will be presented some of these fleets have seen little or no improvement in MTBR whereas some of fleets now enjoy best in class reliability.
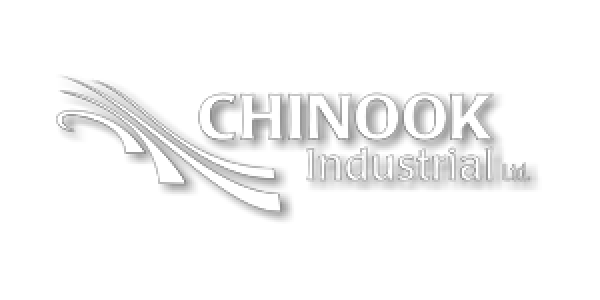
Machinery Grouting Best Practices
TOPIC:
Machinery Grouting Best Practices
INSTRUCTOR(S):
-
Fred’s expertise in technical sales caps a 44-year career with Chinook Industrial Ltd.
His career began as a Red & Blue Seal Machinist involved in the design and manufacture of the Chinook Compressor Valve. Fred’s electrical and mechanical background supported his movement into engineering, providing CNC programing and product design support. During his tenure in engineering, he became involved in quoting and problem solving on Epoxy Grout and Automated Lubrication applications that led to his sales career.
His career has involved him in the Oil & Gas, Marine, Mining, Forestry, and Construction industries with a focus on providing customers with long-term maintenance solutions to improve reliability and decrease costs.
Fred’s field experience is supported by Industry Training including:
- Certified Grout Technician, ITW Performance Polymers
- Certified Coatings Installer, ITW Polymers Sealants
- Five Star Distributor trained in Epoxy and Cementitious Grouts and Coatings
- Automated Lubrication Technician, Lincoln Industrial Corp.
- Automated Lubrication Technician, Graco Lubrication
- SAIT Achievement in Business Competencies
- Dale Carnegie
-
Jason completed the SAIT (Southern Alberta Institute of Technology) Aircraft Maintenance Engineering Technology program in 1992. At the conclusion of the program he achieved placement on the President’s Honour Roll.
Jason began his oil and gas career when he joined the team at Chinook Industrial Ltd in 1993. His role at Chinook Industrial had progressed from customer service representative, Engineering department supervisor, Machine Shop supervisor, Operations Manager and currently Technical Sales Representative. Jason’s roles at Chinook Industrial have included design and manufacture of reciprocating compressor valves, manufacturing drawing and lubrication systems drafting with AutoCAD, CNC programming, grouting project management, grouting and lubrication project quotations, technical assistance and sales support to customers for all product lines offered at Chinook Industrial. He has served as an on-site factory trained representative on many epoxy grouting projects and has also provided epoxy and cementitious grouting training to many of our industry partners. Jason has been a member in good standing of ASET (The Association of Science & Engineering Technology Professionals of Alberta) for 27 years.
His career has involved him in the Oil & Gas, Marine, Mining, Forestry, and Construction industries with a focus on providing customers with long-term, innovative maintenance solutions with the goal of improving equipment reliability and decreasing costs.
Jason’s experience is supported by Industry Training including:
- Certified Grout Technician, ITW Performance Polymers
- Certified Coatings Installer, ITW Polymers Sealants
- Five Star Products distributor trained in Epoxy and Cementitious Grouts and Coatings
- Automated Lubrication Technician, Graco Lubrication
- ASET subject matter expert, Application Review
- Dale Carnegie Course and Dale Carnegie Sales Training
DETAILS:
One (1) hour presentation, including up to 15 min. Q&A
DESCRIPTION:
Best practices for achieving optimum equipment performance from a machinery grout perspective. Equipment reliability is a key component of, and directly proportional to, profitability with today’s industrial producers. Our goal is to educate end users on principles for achieving optimum machinery and equipment reliability and lower operating costs using epoxy machinery grouts and focusing on best installation practices.
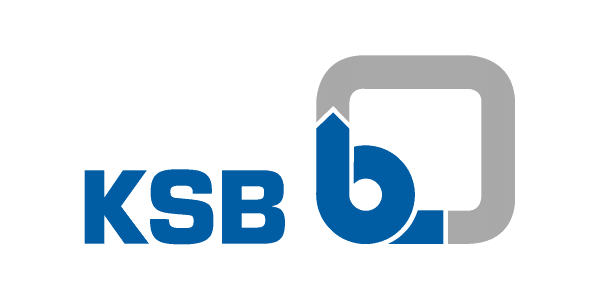
12 Ways to Kill Your Centrifugal Pump
TOPIC:
12 Ways to Kill Your Centrifugal Pump
INSTRUCTOR(S):
-
Siavash is an accomplished professional with over 10 years of experience in the rotating equipment industry. Holding a degree in Engineering from the University of Calgary, he has developed expertise in pump systems and their associated challenges. Throughout his career, Siavash has actively worked on numerous pump projects, gaining knowledge in pump design, installation, and maintenance. His experience includes successfully identifying and resolving various pump failure issues, providing effective solutions to optimize performance and prevent downtime.
DETAILS:
One (1) hour presentation, including up to 15 min. Q&A
DESCRIPTION:
In this presentation, titled "12 Ways to Kill Your Centrifugal Pump," we explore the 12 most common failure modes that can lead to pump malfunctions, such as pipe strain, incorrect operation, and improper clearances. We will discuss how these errors can cause the pump to fail and some tips on avoiding them.

KPI Dashboarding, Issue Identification & Case Study Resolution
TOPIC:
KPI Dashboarding, Issue Identification & Case Study Resolution
INSTRUCTOR(S):
-
Chris Hobbs is a Sr Rotating Equipment Specialist with Pembina Pipeline and has over 22 years experience in the energy transportation and petrochemical refining industries. He specializes in maintenance program development, asset troubleshooting and reliability as well as the application and diagnostics of condition monitoring programs and technologies.
DETAILS:
One (1) hour presentation, including up to 15 min. Q&A
DESCRIPTION:
Pembina Pipeline has recently launched an initiative to maximize the value of its operating installed base (> 1200 pipeline pumps).
This presentation will illustrate the methodology behind the execution of this initiative, as well as the intended benefits in achieving:
Quick adoption and roll out, facilitated by prework in the form of the digitization of Original Equipment Manufacturer (OEM) pump curves for critical assets.
A complete and proactive assessment of asset health.
KPI definition and dashboard development to enable simplified visual identification of asset performance while spotlighting and enabling the prioritization of continuous improvement opportunities.
In addition, the presentation will examine some of the examples / different types of deficiencies observed because of the strategical shift in monitoring strategy, including identification of:
Assets currently not meeting their functional performance standards.
The onset of equipment degradation.
Masked legacy issues.
The reprioritization of maintenance overhauls from one asset to another.
Improved diagnostics to mitigate unplanned outages.

Field techniques for Torsional Vibration Measurements
TOPIC:
Field Techniques for Torsional Vibration Measurements
INSTRUCTOR(S):
-
Wally Bratek is a graduate of the State University of New York at Buffalo and a Principal Consultant in Wood’s vibration, dynamics, and noise group in Calgary, AB.
His more than 25 years of design and field experience include turbomachinery design, acoustical (pulsation) analysis, finite element analysis, machinery diagnostics, rotordynamics and field troubleshooting. Wally has presented at multiple industry conferences including the Gas Machinery Conference (GMC), Vibration Institute Annual Training Conference (VIATC), Calgary Pump Symposium (CPS) and RATS Maintenance Reliability Operation (MRO) conference. He has served on API Standards 618 and 688 committees and is a member of the GMRC Gas Machinery Conference Planning Committee.
DETAILS:
One (1) hour presentation, including up to 15 min. Q&A
DESCRIPTION:
Torsional vibration design analysis (TVA) is essential to ensure the reliability of rotating machinery, particularly when the driver or driven machine is a reciprocating engine or compressor. Since reciprocating machinery torque curves (torque effort) are never flat due to the conversion of the reciprocating motion to rotation and vice-versa, a specialized analysis is required to provide the predicted (calculated) torque curves. As a matter of fact, the alternating component of torque is quite often as much as two to three times greater than the mean, or constant torque during normal operation. Each component in the drive train must be designed to withstand these alternating “rough” torque requirements. Dynamic response due to torsional resonance can amplify these torque levels beyond the fatigue (failure)limits of the individual components.
Even with a successful design analysis, torsional failures may occur due to differences in construction, errors in the TVA modeling information, or changes in machinery loading. The differences between the design (predicted) and real-world (field) operation can and occasionally do lead to major failures and lost production. Since torsional vibration problems often go unnoticed during startup, the failures areusually sudden and occur without prior signs. When a torsional failure does occur, the consequences are significant given the costs and timetoreplace a motor shaft or engine or compressor crankshaft. Unlike lateral vibration that can be detected using typical vibration instrumentation such as accelerometers or proximity probes, measurement of torsional vibration requires specialized instrumentation and approaches.
This presentation is intended for rotating equipment engineers, operators, and millwrights who are responsible for rotating equipment. The goal is to provide guidance to decide when field torsional measurements are appropriate, and to describe techniques for measuring torsional vibration. Methods for torsional vibration measurement using strain gage telemetry, shaft encoders, magnetic pick-ups, laser vibrometers, and optical pick-ups will be described. Relevant statements from industry guidelines will also be presented, including those from API 618 and the GMRC Guideline and Recommended Practice for Control of Torsional Vibrations in Direct‐Driven Separable Reciprocating Compressors. Case studies will be provided to demonstrate approaches for identifying and solving torsional vibration problems before failures occur.

Fugitive Emission Reduction Technologies for Reciprocating Compressors
TOPIC:
Fugitive Emission Reduction Technologies for Reciprocating Compressors
INSTRUCTOR(S):
-
Randy graduated from the University of Calgary in 1990 with a B.Sc. in Computer Science. From 1991 to 2006 he worked in the field of engine and compressor diagnostics developing both portable and continuous monitoring systems. Randy joined HOERBIGER Corporation of America in 2006 providing Project Management for new product introductions. His experience includes Product and Project Management, Manufacturing Engineering, Field Testing, and Product Market introduction. Currently Randy is the North American Valve Product Manager.
DETAILS:
One (1) hour presentation, including up to 15 min. Q&A
DESCRIPTION:
“Methane is the second most abundant anthropogenic GHG after carbon dioxide (CO2), accounting for about 20 percent of global emissions. Methane is more than 25 times as potent as carbon dioxide at trapping heat in the atmosphere. Over the last two centuries, methane concentrations in the atmosphere have more than doubled, largely due to human-related activities. Because methane is both a powerful greenhouse gas and short-lived compared to carbon dioxide, achieving significant reductions would have a rapid and significant effect on atmospheric warming potential.”
https://www.epa.gov/gmi/importance-methane
As a manufacturer of critical infrastructure for the global energy sector, we have an obligation to use our engineering expertise and experience to help mitigate the fugitive emissions of greenhouse gases such as methane from our equipment. In this presentation, we will identify sources of emissions, explore the function of sealing technology, and methods to reduce emissions.

Mechanical Seal Upgrade Helps Nickel Mine Combat Severe Service Conditions
TOPIC:
Mechanical Seal Upgrade Helps Nickel Mine Combat Severe Service Conditions
INSTRUCTOR(S):
-
Stephen has over 30 years of mechanical seal design and trouble-shooting experience. Prior to his role in business development, he spent over 33 years as a sales manager for John Crane. He received his Bachelors in (Mechanical) Engineering and continues to reside in Bedford, Nova Scotia.
DETAILS:
One (1) hour presentation, including up to 15 min. Q&A
DESCRIPTION:
We have prepared a case study from a nickel mine presenting our new mechanical seal for tailings pumps that will use our Upstream Pumping Technology to greatly reduce the need for seal flush water and eliminate high pressure flush water pumps. This design will allow a reduction in water usage/seal from the present 33 l/min, 900 psi max to a requirement of less than 2 l/min, 5 psi max. Upstream pumping technology is a special seal face design that allows us to create what amounts to a high pressure, low volume pump that moves a very small amount of liquid (approx. 0.22 l/min) across the seal faces from a low pressure (approx. 5 psi) source into a much higher pressure liquid area (up to 900 psi) without the use of a high pressure seal support system like a plan 53 or 54 system. This technology was invented by John Crane some years ago and is used widely on high pressure centrifugal gas compressors. We have used it on some lower duty ANSI pump type seals and also on some extreme duty offshore injection pump applications, but this presentation will be one of our early success stories in severe duty mining applications. The spiral groove face design itself has been custom designed by our high pressure sealing group out of the UK. One design will cover the entire range from the first low pressure pump in the train to the final pump with a discharge of up to 900 psi. This design helps to reduce water consumption and improve MTBR under extreme pumping conditions.
This presentation offers practical strategies to help you:
Learn from the challenges faced in a nickel mine tailings pump application using slurry seals with face technology to overcome severe processing duties
Achieve mine KPI productivity goals using mechanical seal strategies to improve reliability
Boost seal MTBR
Maximize critical tailings pump equipment lifecycle
Cut maintenance costs
Avoid unplanned downtime
Reduce water and energy waste during mining process

Laser Cladding Technology
TOPIC:
Laser Cladding Technology
INSTRUCTOR(S):
-
Abdel is the Western Canada Sales Manager and is a Surface Coating Specialist with Castolin Eutectic for 6 years. He is a Materials Engineer by trade, obtaining his degree from McGill University. He also volunteers time for the Moroccan Society of Alberta.
DETAILS:
One (1) hour presentation, including up to 15 min. Q&A
DESCRIPTION:
Laser cladding is a deposition process that is gaining widespread acceptance for restoration of rotating and turbomachinery parts. Laser cladding delivers a higher quality coating material with very little distortion and dilution, as well as enhanced surface quality.
Compared to conventional cladding techniques, it is a valuable precision-driven process which is a to-go solution for the challenging applications when other processes can’t be used. For example, all fusion welding processes generate a heat affected zone and the properties in that region are unlikely to meet base metal requirements without a postweld heat treatment. This is significantly important when the base material is quenched and tempered steel, which is commonly used for turbomachinery shafts. However, with laser cladding post-weld heat treatment usually is not required due to low heat input of the process, which greatly reduces the size of the heat affected zone.
It is important to understand the basic capabilities, limitations, and potential pitfalls of the laser cladding process, and how it should be qualified to ensure that laser weld repairs meet requirements for the given application. Therefore, as a case study for restoring rotating/turbomachinery part, we will discuss the challenge as well as solution and outcome of a key component in the O&G industry.
Plungers in pumps and compressors exhibit rapid surface wear. These components had previously been coated using HVOF process. Using laser cladding process with proprietary alloy, we managed provide a higher wear resistance and at least double the service life when compared to HVOF coating.

Installation & Alignment - How to Flatten The Infant Mortality Curve
TOPIC:
Installation & Alignment - How To Flatten The Infant Mortality Curve
INSTRUCTOR(S):
-
Roman Megela Gazdova works as Reliability Engineer at Easy-Laser AB. Roman has more than 20 years of experience in assembly, commissioning and service of gas compression systems all over the world, from Europe to Asia and USA. From glass production, stainless steel production, oil and gas, oxygen, petrochemical, natural gas, biogas, hydrocarbons. Vibration specialist certificate CAT 1.
Mechanical Engineering background with specialty of optimizing productions processes. Now, Roman is on the mission to teach good practice for reliable machinery installation through Reliability language.
DETAILS:
One (1) hour presentation, including up to 15 min. Q&A
DESCRIPTION:

Rotating without Maintenance - Maintenance-Free Couplings
Topic:
Rotating Without Maintenance - Maintenance-Free Couplings
Instructor(s):
-
Patrick has a large knowledge of the industry as he’s been in the business for more than 40 years servicing and helping find solutions to many rotating equipment applications.
Patrick has been with Renold for more than 10 years.
-
Helene has 40 years’ experience in the industrial business and has been with Renold for the last 31 Years. Helene specializes in these coupling products, has performed a multitude of training classes across the country, and is the go-to person when it comes to coupling applications.
Details:
One (1) hour presentation, including up to 15 min. Q&A
Description:
Our representatives will be presenting our Hi-Tec coupling series as well as our PM Series. The RBI coupling is a perfect fit for all industrial applications, the main features of the Hi-Tec series are: a maintenance-free coupling, vibration control, zero backlash and many other features that helps having a rubber-in-compression coupling. The PM Series, another excellent option for all industrial applications can be suitable for shaft diameters up to 32 inches.
Renold will demonstrate the reliability of these couplings, the excellent opportunity for cost savings, and how they are suitable for a large variety of industries, such as; metal manufacturing, mining, fans, compressors, cranes and hoists and many more.

The When, Why and How of The High Velocity Oil Flush
Topic:
The When, Why and How of The High Velocity Oil Flush
Instructor(s):
-
-
18 years in the Industrial Oil Analysis business, and now determining the root causes of equipment problems to addressing them.
Details:
One (1) hour presentation, including up to 15 min. Q&A
Description:
Consistency is the key to success. This is true with sports, skills, and the maintenance of industrial rotating equipment. Part of good maintenance is using the High Velocity Oil Flush to clean equipment internals and ensure you get the most out of your equipment through a long and healthy life cycle. Turbulent flow, heat and vibration are just some of that major factors that contribute to an effective oil flush. Follow the journey of a piece of equipment, from commissioning, to maintenance, to end of life discussing the function of the lubricant, the root causes of problems, how oil analysis is used to monitor condition and how an oil flush can help you get the most out of your equipment.

Oil-Free H2 Compression Challenges & Solutions
Topic:
Oil-Free H2 Compression - How to Solve the Challenge of Delivering Large Mass Flow & High-Pressure & Long MTBO
Instructor(s):
-
-
Johann has worked for Burckhardt for over 12 years in various strategic business development, sales, and management roles, based in Edmonton. He graduated from the University of Alberta with a Bachelor’s Degree in Mechanical Engineering.
Details:
One (1) hour presentation, including up to 15 min. Q&A
Description:
Mr. Oliver Franz with Burckhardt’s hydrogen compressor group works closely with Mr. Johann Scherer-Brown in this booming market. Together they will present advancements in the emerging hydrogen market, which is particularly active in Alberta.

See and Hear 3-Types of Pump Cavitation
Topic:
See and Hear 3-Types of Pump Cavitation
Instructor(s):
-
Stefan Fediw has been in the fluid transfer industry for almost 25 years. In that time he has worked for several pump manufacturers along with equipment distributors. For many years, Stefan also taught several Millwright (night-school) College courses. In his current position, with John Brooks Company, he works closely with Consulting Engineers on pumping projects and is also heavily involved in maintenance training for Municipal and Industrial Equipment Operators.
Details:
One (1) hour presentation, including up to 15 min. Q&A
Description:
This presentation is an overview of the 3-types of cavitation within a centrifugal pump. Along with PowerPoint slides, there will be an actual "glass-face" pump to demonstrate all the forms of cavitation within the pump. Discussions will also focus on mitigation and elimination of cavitation.

High Performance Pistons – Optimizing Run-time and Predicting Performance
Topic:
High Performance Pistons – Optimizing Run-time and Predicting Performance
Instructor(s):
-
John Ladd is the Engineering Manager at HOERBIGER Service Inc. based in Houston, TX. He supports the North America service branches providing repairs and upgrades on Reciprocating Compressors for the Oil & Gas and Chemical/Petrochemical industry. Prior to his current role he was a Solutions REE Engineering Specialist and Compressor Analyst at HOERBIGER Service Inc. John earned his Master's in mechanical engineering at Colorado State University with a focus on legacy integral pipeline compressors.
Details:
One (1) hour presentation, including up to 15 min. Q&A
Description:
Reliability and performance related issues of pistons and cylinder rings can be avoided in the vast majority of cases and the piston should not be the MTBF (Mean Time Before Failure) bottle neck. Even for some non-lube machines a piston layout can be designed that results in a five year uninterrupted run-time (as discussed in one of the cases in this paper). Piston performance and reliability is highly predictable. In most cases poor reliability of cylinder rings stems from incorrect application of particular ring designs, insufficient engineering or off-the-shelf methods.
A new design process has been developed to mitigate reliability bottle-necks on reciprocating compressor pistons. The first pistons that have been engineered using this process were installed 2015. This paper presents a general guideline for the design of high performance pistons and a case study that validates the methods applied. The main topics are:
The piston layout optimization process
The details of the changes from an existing to a new design.
Inspection of worn cylinder rings and quantifying the wear rate.
Comparison the measured wear rate to the prediction of the model that was used during the design and engineering phase

Building a Business Case for Maintenance & Reliability Improvement
Topic:
Building a Business Case for Maintenance & Reliability Improvement
Instructor(s):
-
is the author of "Root Cause Analysis Made Simple – Driving Bottom Line Improvements by Preventing One Failure at a Time". She specializes in asset management and reliability strategy, cost effective lean maintenance programs, and operational excellence. With a keen interest in building competency and capability in client staff, Susan brings over 25 years of progressive experience to drive asset management, reliability, and maintenance business decisions, and to implement improvement opportunities in asset intensive 24 x 7 x 365 production companies primarily in the commodity sectors.
Details:
One (1) hour presentation, including up to 15 min. Q&A
Description:
With today’s continued emphasis on delivering value from our assets while balancing cost, risk and performance, the need to understand the business contributions from maintenance activities has never been higher. This session will focus on ‘Building the Business Case for Maintenance and Reliability Improvement’. The intended audience of this presentation will be involved in day to day maintenance and reliability functions at their facility, such as millwright leads, rotating equipment specialists, and Engineers.
Topics include:
Moving from a reactive to proactive maintenance culture – breaking down the silos, introducing PdM methodologies
Contributions of proposed maintenance improvement activities to meeting organizational goals and objectives
Quantifying the contributions of maintenance improvement (i.e. increased availability, increased throughput, decreased OPEX per unit of production)
How to get started on your improvement journey

Electrification and Modernization of Reciprocating Compressors
Topic:
Electrification and Modernization of Reciprocating Compressors
Instructor(s):
-
More than 15 years of experience specializing in rotating equipment design and service, with a strong focus on reciprocating compressors. Presently leads the technical services department, specializing in machine revamps, upgrades, troubleshooting, RCA, component fatigue and field service support. Beyond the machine he is an expert in problem solving issues related to vibration, acoustical pulsation and fatigue of piping and structures.
Details:
One (1) hour presentation, including up to 15 min. Q&A
Description:
-Identify potential failure modes and forces that cause them
-API 618 Pulsation and Torsional studies (what are they and why they need to be done)
-Coupling selection and Dampening (Campbell diagrams and how they work)
-Example of component failures and solutions
-Case study

Mobile Augmented Reality Services
Topic:
Mobile Augmented Reality Services (M.A.R.S.)
Instructor(s):
-
Nick is experienced with Automated Systems Design and Engineering, PLC Programming and Installation, HMI Programming, Augmented Reality, as well as Commissioning and Maintenance.
Nick has spent 14 years at Surepoint Group in various roles such as Software Development Engineer, Field Services Engineer, and currently as Control Systems Engineer.
Nick holds a Bachelor of Science in Computer Engineering from the University of Alberta.
Details:
One (1) hour presentation, including up to 15 min. Q&A
Description:
Leveraging the power of the Microsoft HoloLens 2, companies can connect with their workers and industry experts on any job site remotely utilizing hand-free 2-way voice and video collaborations.
The Hololens 2 is the most advanced augmented reality device in the industry and allows workers on any job site to connect with their teams and colleagues in a variety of applications.
Remote Worker Assistance
Design and Place
Training and Technical Support
Visualize Your Ideas
The presentation will include a live demonstration of the technology at work plus a case study where inspectors are able to witness project progress with a guided walk through of a facility remotely without having to travel to site.

Root Cause Failure Analysis
Topic:
Root Cause Failure Analysis
Instructor(s):
-
Chris provides bearing related equipment design and maintenance expertise to many of Canada’s resource based industries. He started with NTN in 2002 with a background in material handling equipment design. Focusing on Petroleum, Mining and the Pulp and Paper industry, Chris is very familiar with applications in extreme operating conditions.
-
James completed a Bachelor of Science degree in 1999 from the University of Alberta and subsequently spent 18+ years in territory management and technical sales.
Details:
One (1) hour presentation, including up to 15 min. Q&A
Description:
Regardless of industry, one reality is that demands on rotating equipment result in demands directly on the bearings. Join the NTN Technical Engineering And Maintenance TEAM for a discussion on root cause failure analysis.
A major component of any effective preventative maintenance program is understanding what went wrong...and then correcting the problem. Bearing failure analysis is a pro-active, front line job that has proven to increase equipment up-time. In this lecture, we will review the most common rolling element bearing failure modes and causes.
Following the lecture, there will be a demonstration of NTN diagnostics services utilizing our INSYNC remote diagnostics service to show a failure review in real time from our diagnostic lab.
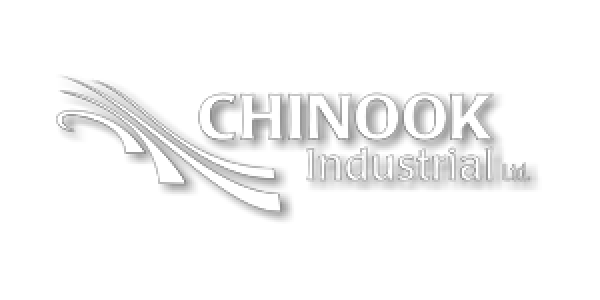
Machinery Grouting Best Practices to Optimize Equipment Performance
Topic:
Machinery Grouting Best Practices to Optimize Equipment Performance
Instructor(s):
-
Jason has worked for Chinook Industrial for a total of 27 years, bookending a 2-year hiatus. Jason is a seasoned management professional as well as a technical sales rep with experience in such things as compressor valve manufacturing & reconditioning, grouting & coating systems, and lubrication systems. He graduated from SAIT with a diploma in Aircraft Maintenance Engineering Technology.
-
Fred’s expertise in technical sales caps a 35 year career with Chinook Industrial Ltd.
Beginning as a Red & Blue Seal Machinist involved in the design and manufacture of the Chinook Compressor Valve. Fred’s electrical and mechanical background supported his movement into engineering providing CNC programing and product design support. During his tenure in engineering he became involved in quoting and problem solving on Epoxy Grout and Automated Lubrication applications that led to his sales career.
His career has involved him in the Oil & Gas, Marine, Mining, Forestry, and Construction industries with a focus on providing customers with long-term maintenance solutions to improve reliability and decrease costs.
Details:
One (1) hour presentation, including up to 15 min. Q&A
Room name and time slot TBD
Description:
Presenting best practices for achieving optimum equipment performance from a machinery grout perspective. Equipment reliability is a key component of, and directly proportional to, profitability with today’s industrial producers. Our goal is to educate end users on principles for achieving optimum machinery and equipment reliability and lower operating costs using epoxy machinery grouts and focusing on best installation practices.

Turbine Rotordynamic Instability at CAES Facility
Topic:
Resolution of Expansion Turbine Rotordynamic Instability at a Compressed Air Energy Storage (CAES) Facility
Instructor(s):
-
Wally Bratek is a Principal consultant in Wood’s vibration, dynamics and noise group. His more than 20 years design and field experience include acoustical (pulsation) and mechanical vibration analysis, machinery diagnostics, field testing and troubleshooting, alignment, high-speed balancing, lateral rotordynamics and piping flexibility.
Wally has presented multiple papers at industry conferences including the Gas Machinery Conference (GMC) and Vibration Institute Annual Training Conference (VIATC). He has served on API Standards 618 and 688 committees and is a member of the GMRC Gas Machinery Conference Planning Committee.
Details:
One (1) hour presentation, including up to 15 min. Q&A
Description:
Renewables can provide economical carbon-free electricity, but due to inconsistent weather, power from solar and wind is intermittent. Technologies that can temporarily store electricity to firm-up the supply from renewables will allow electricity grids to meet energy demand with a lower carbon footprint. In compressed-air energy storage, excess renewable electricity is used to run compressors that inject air into underground caverns. When electricity is needed, the compressed air is expanded through turbines to generate electricity. A water injection system moderates the pressure in the cavern and allows the machinery to operate at consistent operating pressures.
This case study focuses on rotordynamic instability that was experienced on one of the expansion turbine stages during commissioning of a compressed air energy storage (CAES) facility in Ontario, Canada. The turbine which experienced the vibration is a two-stage, integrally geared, radial turbine powered by heated compressed air and coupled to an 1,800 kW induction generator. The turbine rotor is equipped with tilt-pad bearings and operates at 42,000 RPM.
Broad-spectrum sub-synchronous vibration was experienced on the rotor during the initial runs, which was determined to be due to aerodynamic instability. The vibration caused the turbine to trip prior to reaching the full power operating condition. Swirl brakes, a flow straightener in the turbine exhaust, and reduced bearing oil supply temperature were implemented during commissioning with limited improvements to rotor stability. The thrust balance pressure and resulting thrust load also showed only a minor influence on rotor stability.
The rotordynamic simulation model was then investigated to duplicate the field test results and determine potential design or operating changes to increase the stability margin. The original rotor model confirmed marginally stable results at the design operating conditions. However, subsequent analysis determined that start-up operating conditions resulted in reduced stability margin.
Experimentation in the field established that with careful control of the turbine inlet variable nozzles that manage mass flow and interstage pressures, as well as manual control of impeller thrust balance pressure, successful operation to full power could be achieved without a vibration trip. Ultimately, automation and tuning of turbine inlet nozzles and thrust balance pressure allowed the turbine to be routinely started and operated to full power while avoiding or quickly passing through unstable operation.
The rotordynamics model was also used to design a squeeze-film damper bearing to significantly improve the stability margin. The new bearing was procured, along with an optimized swirl brake, and these items are available as a precaution to be installed if stability problems reappear in the future.

Mechanical Seal Plan 54 for Severe Duty Application
Topic:
Mechanical Seal Plan 54 for Severe Duty Application
Instructor(s):
Chris Ausford, Engineering Manager, John Crane
Bryce Dreger, Engineering Specialist
Details:
One (1) hour presentation, including up to 15 min. Q&A
Description:
Dual-pressurized mechanical seals can provide the highest level of safety and equipment uptime. Achieving this potential however, typically requires a more elaborate support system and thus more complex consideration from initial design to long-term operation. The API Plan 54 External Pressurized Barrier System is the most widely misunderstood of all options but with the correct design and implementation, this approach can deliver unmatched reliability in virtually any application. An exceptional partnership between John Crane and Enbridge over the past 6 years has resulted in the development of a highly successful Plan 54 solution for severe operating conditions with implications that could improve understanding and reliability of these systems across all industries. This presentation will share some of the key learnings and optimization tactics discovered through a case study of this unique design and application.
-
Chris graduated from the University of Alberta with a B.Sc. in Mechanical Engineering. Joined John Crane in 2007 as an Applications Engineer in the First Fit Projects group, eventually moving into a Technical Sales position looking after customers in mining, oil & gas, pulp & paper, OEM, and pipeline. With nearly 15 years’ experience in the rotating equipment industry, Chris now leads the engineering team for John Crane Canada with 10+ engineers spread across the country in Quebec, Ontario, and Alberta.
-
Bryce graduated from the University of Alberta with a Petroleum Engineering degree in 1985. He has spent 35 years focused on rotating equipment within a wide range of industries. Although his specialty is mechanical seals and sealing systems, he has spent the last 15 years working with a broad range of pumping equipment – currently as a Pump SME for Enbridge Pipelines. He has touched every facet of the industry from design, procurement, commissioning, operations, maintenance, and troubleshooting. He enjoys spending time with his family; a wife, 4 children and 4 grandchildren. He also tries to travel as much as possible.

Torsional Vibration Solutions
PRESENTERS
Bob Whitney
Bob is the Innvoations Director for Riverhawk Company based out of Whitesboro, New York.
Earl Boyd
Earl is the proprietor & president of Solutions 4ltd. His 45 years of experience in Industrial Power Transmission encompasses all aspects of business: planning, engineering, sales, marketing, senior management and directorships.
SUMMARY
Torsional vibration occurs often within shaft strings. In many cases the equipment runs well and tolerates the torsional vibration for long and dependable operation. On occasion torsional vibration developed within shafts that are not designed to tolerate it. Trouble can show up in a number of ways depending which part of operation is the most sensitive to torsional vibration.
Here is a short list of ways that torsional vibration can manifest:
Process variations such as sheet thickness in rolled products.
Fretting of joints leading to sloppy fits and wearing of components.
Lateral vibration where torque causes such movements, for example gear shafting.
Fatigue of shafting components which is notorious for sudden unexpected failures.
Structural overload, when torque values climb to levels that yield shaft material.
None of these results are desirable. When we become aware that a torsional problem exists we first need to learn a little bit about the nature of the vibration before a proper solution can be selected. Torsional vibration comes in a number of forms, each requiring a particular type of solution.
This presentation will discuss a number of torsional vibration types and attempts to describe their nature in a way that can be understood. It then discussed a series of solution approaches, describes how each addresses issues and provides some guidance on which solution types might work best for torsional vibration type.
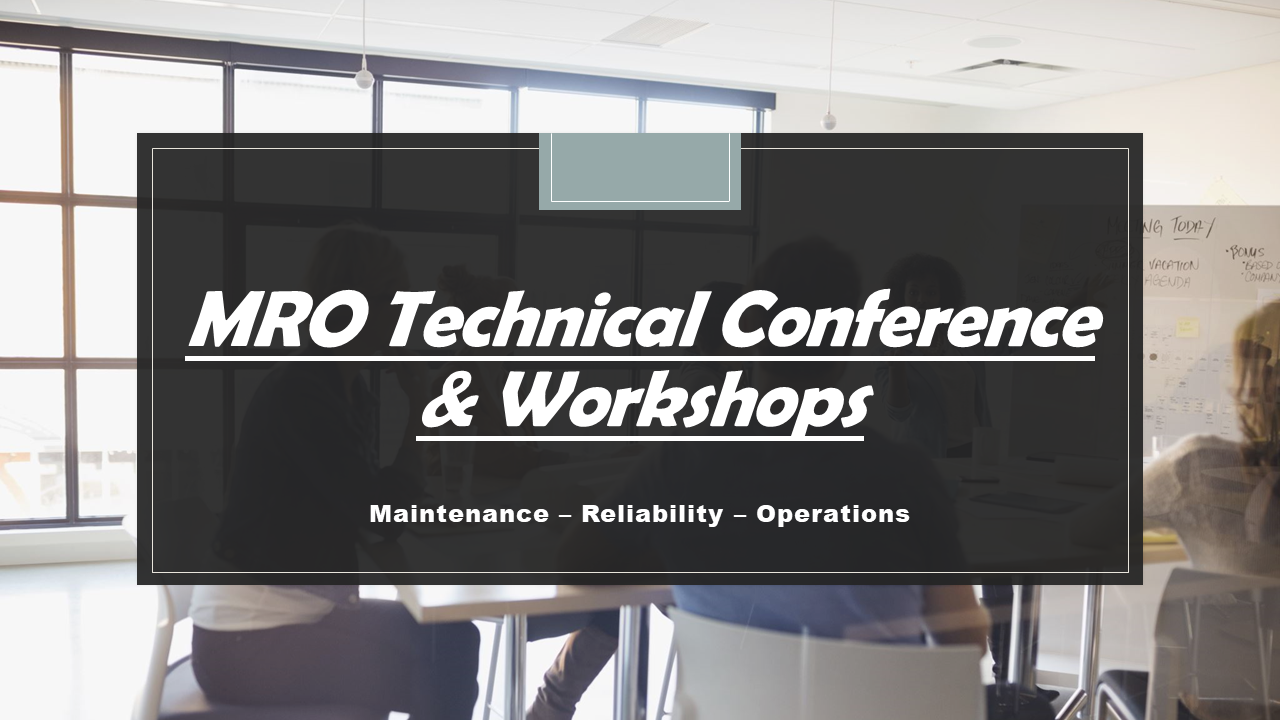
Reciprocating Compressor Piston Rod Packing Types, Design, and Failures
PRESENTER
David Flood
Burckhardt Compression is one of the worldwide market leaders in the field of reciprocating compressors. Since 1844 Burckhardt's highly skilled workforce has crafted superior solutions and set the benchmark for the gas compression industry.
SUMMARY
Rings and packing are very critical components that ensure reciprocating compressors operate properly. In this presentation, we will explore the different factors that make well designed rings and packing.
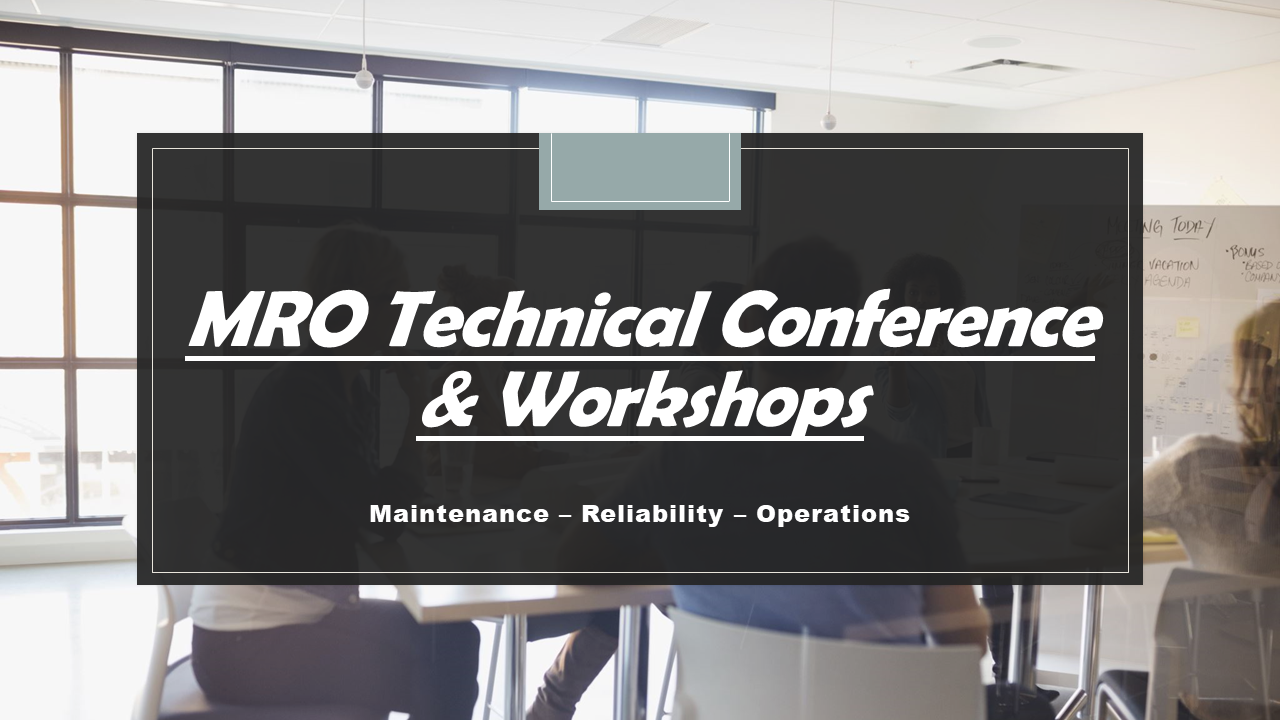
Vane-Pass Resonance, Analysis & Resolution on a 3000 HP BB1 Pump using Modal/ODS & FEA
PRESENTER
Monroe Voyles
Monroe Voyles is a mechanical engineer with 23 years of experience; 7 in a chemical plant, 3 in a refinery, 9 as a pump improvement engineer for Flowserve, and 4 as a Solutions Engineer for ITT Goulds Pumps. Experience with large electric motors, gas turbines, centrifugal compressors, reciprocating compressors, steam turbines, large API pumps, ANSI pumps, high pressure boiler feed water pumps, non-contacting gas seals, high temperature bellows seals, mag-drive pumps, liquid ring compressors, cooling tower fans/gear boxes, and large compressor gear boxes. Work included RCFA, Vibration analysis, performance testing, and upgrading systems/equipment to resolve problems. Proficient with finite element modeling (CREO/Simulate).
SUMMARY
Most centrifugal pumps create vane-pass pressure pulsation and vibration as a normal reaction to head generation. In some cases the resulting vane-pass vibration amplitudes can be excessive. The cause of high vibration amplitudes can be related to large pressure pulsation forces; resonance can also amplify the vibration response in some cases.
This case study describes excessive vane-pass vibration amplitudes that were caused by structural and possibly acoustic resonance. The solution involved pump modifications to decrease vane-pass pressure pulsation amplitudes and a speed change to increase frequency separation margin between vane-pass frequency and natural frequencies. ODS and Modal data was used to evaluate the natural frequencies and mode shapes. Modal data was also used to calibrate a finite element model. Finite element analysis was used to evaluate the pump/piping system. Several previously planned (costly) actions were also shown to be ineffective; therefore, a planned outage scope was changed due to this analysis. The result was a dramatic reduction in vibration amplitudes and noise with minimal cost.
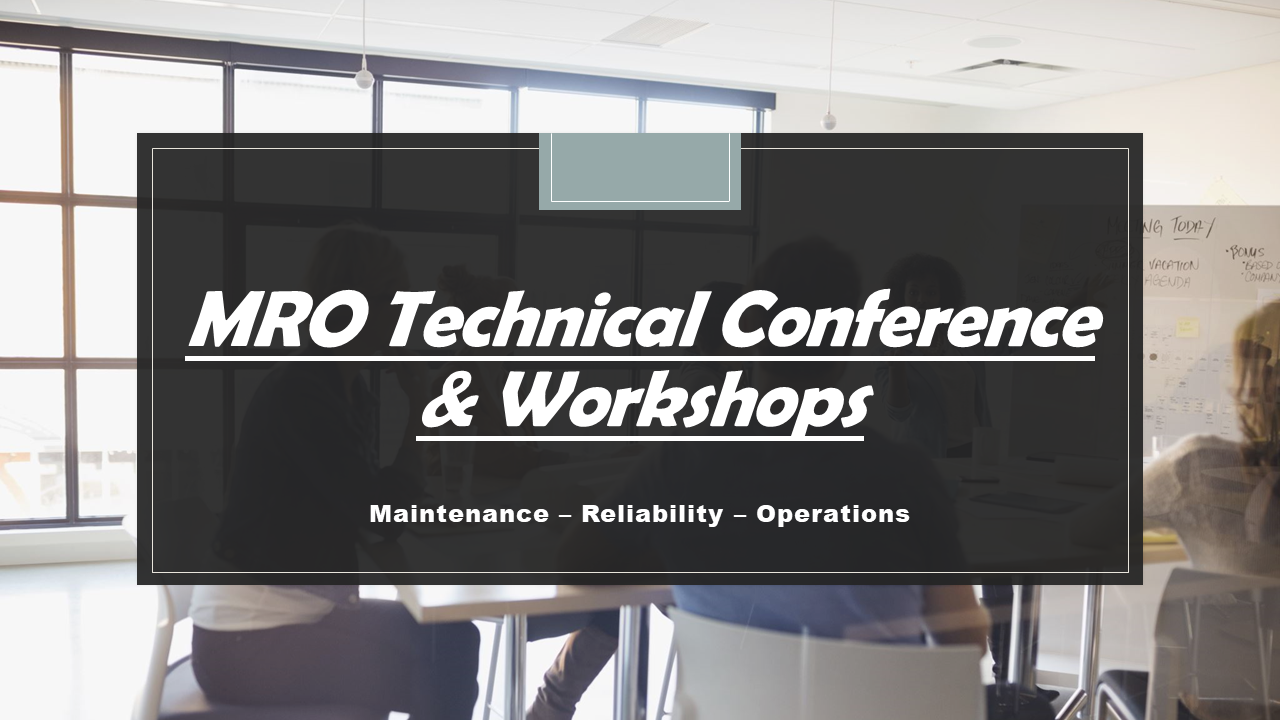
Pump Components Repair Using Polymeric Products: Case Study
PRESENTER
Dr.Kofi Freeman Adane
Dr. Adane is a Senior Research Engineer at Fluid Systems Engineering, InnoTech Alberta Inc, a subsidiary of Alberta Innovates, Edmonton. Primarily, he leads industry driven research and technology development (R&TD) projects on pipeline systems. He is a lead author for “Slurry Pipeline Handbook” for oil sands industry through Materials and Reliability in Oil Sands (MARIOS) consortium. Prior to his current position, he held several positions in industry and academia. Most recently, Dr. Adane worked for Saskatchewan Research Council, Saskatoon where he served as a lead engineer in the construction of its High Pressure and High Temperature volatile loop to model steam-assisted gravity drainage (SAGD) operations and also contributed to the development of the “SRC Tailings Manual” for Canada’s Oil Sands Innovation Alliance (COSIA). He holds degrees in mechanical engineering with PhD from University of Manitoba, Winnipeg. Dr. Adane has strong expertise in fluid engineering systems, specifically piping and pumps, and he is a registered professional engineer in province of Alberta.
SUMMARY
There are significant costs associated with maintaining and owning centrifugal pumps in oil and gas, chemical, mining and oil sands facilities. In some of these industries, the fluid might contain particulates or solids being intentional as products or process, or unintentional. The presence of these particulates or solids can accelerate wear (erosion, corrosion or both) in the pump, which usually lead to decreased performance and/or wear or service life. When such situations occur, owners or operators are faced with capital expense for its replacement. Another temporary solution is to attempt to repair specific component (s).
We have a pilot-plant which was designed to test piping components, and perform several fluid flow testing services. Therefore, unlike a typical production or process plants where they are designed for specific conditions, our plant is an agile, technology test bed and used for several different conditions including to assessment of wear life. Therefore, our pump has shorter wear life than comparable pump in production facility. Faced with capital expense, we opted to explore the repair solution.
There are several vendors who offer repair kits for pumps and other piping systems. We purchased one of these kits to repair our slurry pump. This presentation will discuss the lessons learned and some recommendations. Our experience is being used in oil sands mining industry. Sharing this experience will be beneficial to any industry using centrifugal pumps.

Fundamentals of Vibration Problem Solving
PRESENTER
Wally Bratek
Wally Bratek is a principal consultant in Wood’s vibration, dynamics and noise group. His more than 20 years’ design and field experience include acoustical (pulsation) and mechanical vibration analysis, machinery dynamics, field testing and troubleshooting, alignment, high-speed balancing, lateral rotordynamics, piping flexibility and flow-induced pulsation. Wally has presented multiple papers at industry conferences, is a member of the GMRC Gas Machinery Conference Planning Committee, and is an active member of the API 618 6th Edition task force or pulsation analysis.
SUMMARY
Technologies and hardware for the measurement and diagnosis of vibration on machinery and piping systems continue to evolve. Multi-channel data acquisition systems (48 or more) have become commonplace whereas simple one- or two-channel systems have been the standard for many years. More-efficient software is available to analyze and visualize the mountain of data that is collected. However, the use of advanced tools is not a substitute for careful examination of basic factors that might cause increased vibration levels. In many cases, basic observations and analysis can lead to the identification of causes without having to resort to more costly field measurements or advanced analyses. Sometimes a “back-to-basics” analysis approach is all that is required to solve a problem.
This presentation is intended for plant engineers, operators and millwrights who are often the first to identify vibration problems and asked to solve them. The goal of this lecture is to present the fundamentals of vibration, typical causes for vibration issues and common remedies. Techniques for visual inspections are presented.
Case studies involving pumps and compressors will be discussed to show how seemingly complex issues can be solved based on knowledge of basic vibration principles. Attendees will gain valuable knowledge of vibration basics and simple approaches for solving problems.

Do we send this out, or rebuild it in our shop? Analysis of Today’s Maintenance Strategy
PRESENTER
Mark Tinis
Mark is the branch manager for Mi TechCan Services in Edmonton, a Division of Motion Canada. Mark has 24 years of experience with two different industry leaders in the heavy industrial and mechanical services sector.
SUMMARY
Machinery rebuild philosophies are constantly changing. It’s often hard to decide where crucial plant mechanical staff should be focusing their energy. “Should we be repairing this critical machine in our own shop, or sending out to a local service provider?” It’s a difficult question, but an important one. In this discussion, we will explore the advantages and disadvantages of all the options. We know the decision is never cut and dried and many factors contribute to your resulting verdict:
How critical is this machine to our operation?
How important is it that our staff understand every nut and bolt in it?
Do we have the in house knowledge to do the job right?
Who are the experts, and how do we leverage them to ensure a quality rebuild?
Do we have the right tools?
Is there other work in the plant that requires our people’s attention?
How do we reduce our overall cost of ownership?
We will explore and discuss all of these questions and more in this dynamic breakout session. Attendees are highly encouraged to actively participate in this session.