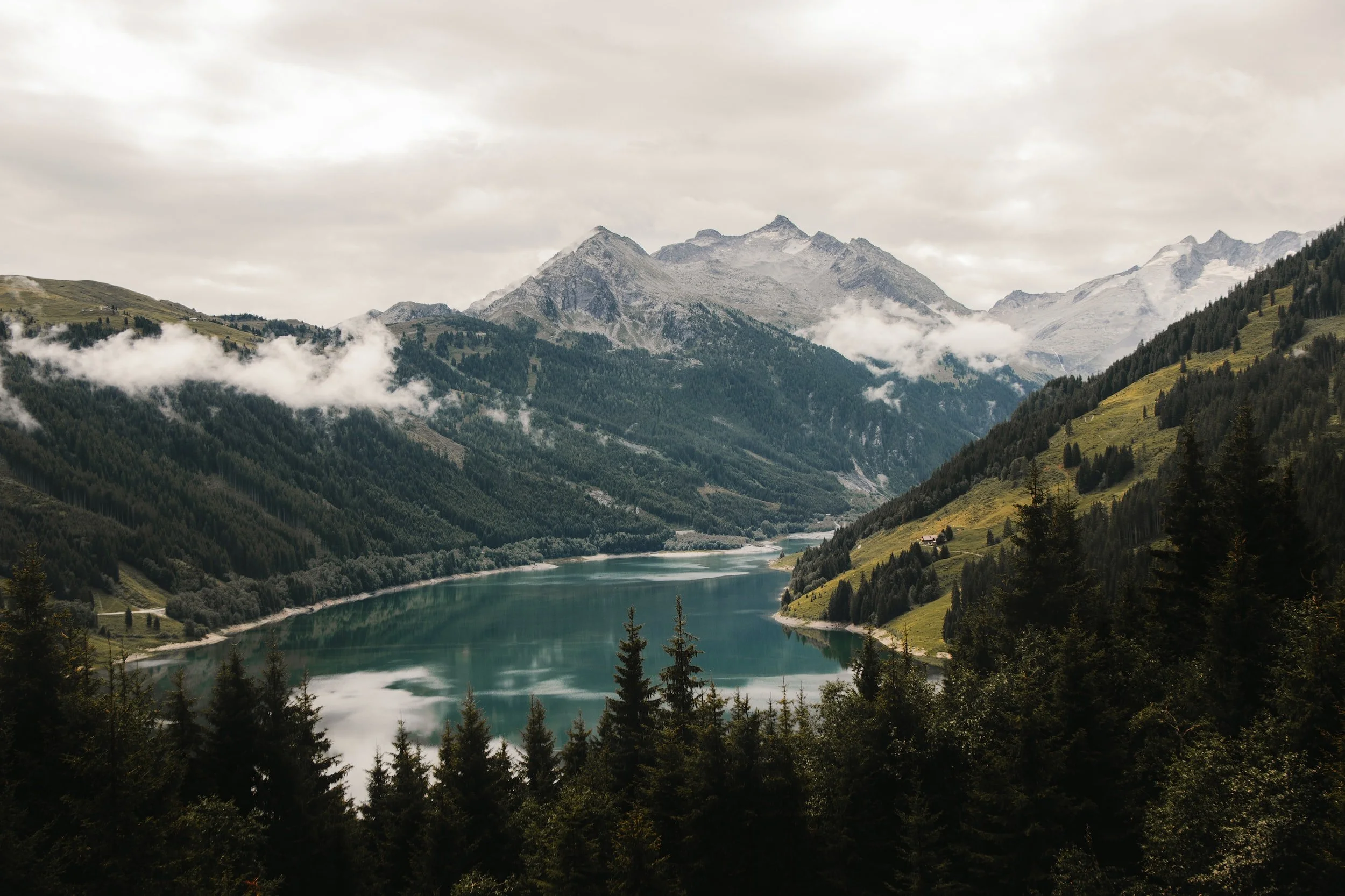
RATS MRO Conference
Presentation ARchive
2023 Presentations
2022 Presentations
2018 Presentations
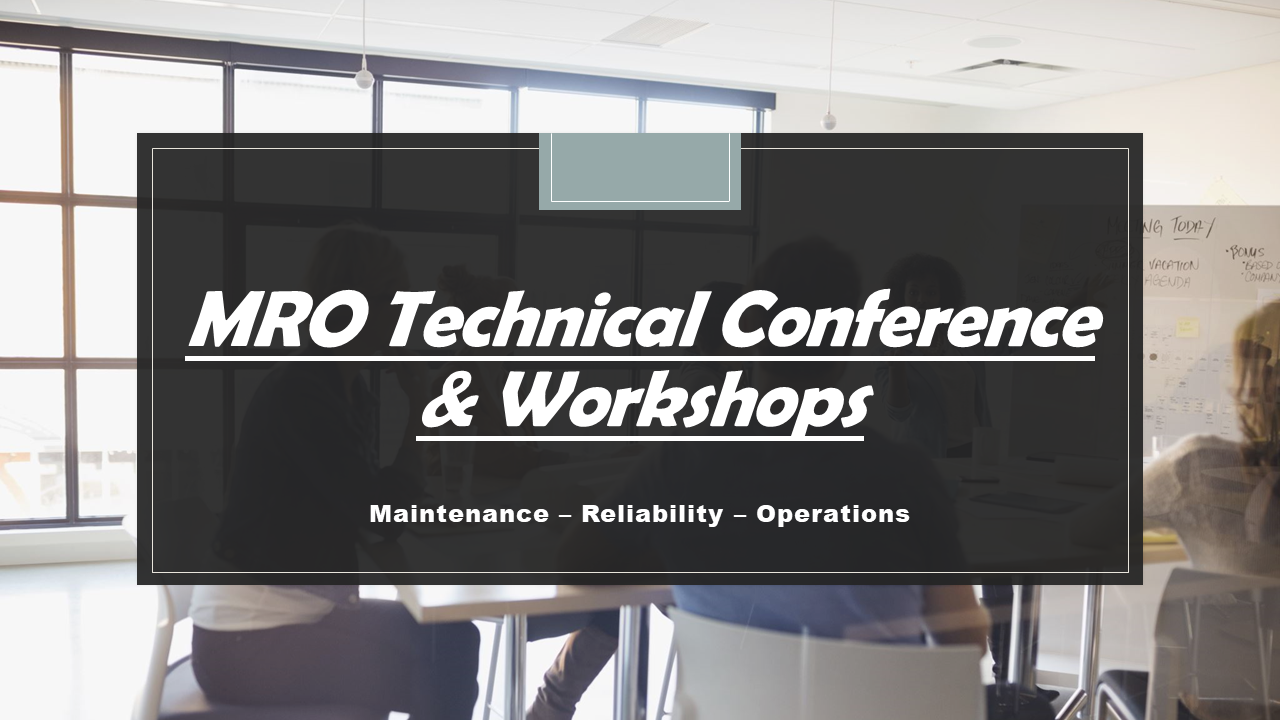
Vane-Pass Resonance, Analysis & Resolution on a 3000 HP BB1 Pump using Modal/ODS & FEA
PRESENTER
Monroe Voyles
Monroe Voyles is a mechanical engineer with 23 years of experience; 7 in a chemical plant, 3 in a refinery, 9 as a pump improvement engineer for Flowserve, and 4 as a Solutions Engineer for ITT Goulds Pumps. Experience with large electric motors, gas turbines, centrifugal compressors, reciprocating compressors, steam turbines, large API pumps, ANSI pumps, high pressure boiler feed water pumps, non-contacting gas seals, high temperature bellows seals, mag-drive pumps, liquid ring compressors, cooling tower fans/gear boxes, and large compressor gear boxes. Work included RCFA, Vibration analysis, performance testing, and upgrading systems/equipment to resolve problems. Proficient with finite element modeling (CREO/Simulate).
SUMMARY
Most centrifugal pumps create vane-pass pressure pulsation and vibration as a normal reaction to head generation. In some cases the resulting vane-pass vibration amplitudes can be excessive. The cause of high vibration amplitudes can be related to large pressure pulsation forces; resonance can also amplify the vibration response in some cases.
This case study describes excessive vane-pass vibration amplitudes that were caused by structural and possibly acoustic resonance. The solution involved pump modifications to decrease vane-pass pressure pulsation amplitudes and a speed change to increase frequency separation margin between vane-pass frequency and natural frequencies. ODS and Modal data was used to evaluate the natural frequencies and mode shapes. Modal data was also used to calibrate a finite element model. Finite element analysis was used to evaluate the pump/piping system. Several previously planned (costly) actions were also shown to be ineffective; therefore, a planned outage scope was changed due to this analysis. The result was a dramatic reduction in vibration amplitudes and noise with minimal cost.

Fundamentals of Vibration Problem Solving
PRESENTER
Wally Bratek
Wally Bratek is a principal consultant in Wood’s vibration, dynamics and noise group. His more than 20 years’ design and field experience include acoustical (pulsation) and mechanical vibration analysis, machinery dynamics, field testing and troubleshooting, alignment, high-speed balancing, lateral rotordynamics, piping flexibility and flow-induced pulsation. Wally has presented multiple papers at industry conferences, is a member of the GMRC Gas Machinery Conference Planning Committee, and is an active member of the API 618 6th Edition task force or pulsation analysis.
SUMMARY
Technologies and hardware for the measurement and diagnosis of vibration on machinery and piping systems continue to evolve. Multi-channel data acquisition systems (48 or more) have become commonplace whereas simple one- or two-channel systems have been the standard for many years. More-efficient software is available to analyze and visualize the mountain of data that is collected. However, the use of advanced tools is not a substitute for careful examination of basic factors that might cause increased vibration levels. In many cases, basic observations and analysis can lead to the identification of causes without having to resort to more costly field measurements or advanced analyses. Sometimes a “back-to-basics” analysis approach is all that is required to solve a problem.
This presentation is intended for plant engineers, operators and millwrights who are often the first to identify vibration problems and asked to solve them. The goal of this lecture is to present the fundamentals of vibration, typical causes for vibration issues and common remedies. Techniques for visual inspections are presented.
Case studies involving pumps and compressors will be discussed to show how seemingly complex issues can be solved based on knowledge of basic vibration principles. Attendees will gain valuable knowledge of vibration basics and simple approaches for solving problems.

Design and Installation Considerations for Proper Anchoring of Rotating Machinery
PRESENTER
Christopher Ewald
Christopher Ewald joined ITW Engineering Polymers in 2015. His primary responsibilities include technical support and educating personnel in engineering, construction, operations and maintenance on best practices and recommendations for epoxy design and installation. His primary focus is on Industrial applications and US Military Marine installations, and a secondary focus on all marines applications. He holds a degree in Civil & Environmental Engineering from the Georgia Institute of Technology.
SUMMARY
Proper consideration for the design and installation of anchoring of rotating machinery is key to the long-term integrity and reliability for the entire foundation system. As a key component in the foundation system, bolt or adhesive failures result in a loss of connection to the foundation that will cause a significant increase in operating vibrations of equipment, leading to a decreased life span and reduced mean time between failures.
This presentation will discuss potential failures that may occur in the connection of the equipment to the foundation, methodology for diagnosis of potential failures, best practices and techniques for remediating failures after occurrence, and prevention recommendations for avoidance of issues. Bolting configurations and specific methodology for ensuring proper bolt tensioning and anchoring will be discussed. Finally, a case study showing the diagnosing and remediation of a failed anchor system that was conducted without necessitating the removal of the machinery is presented.
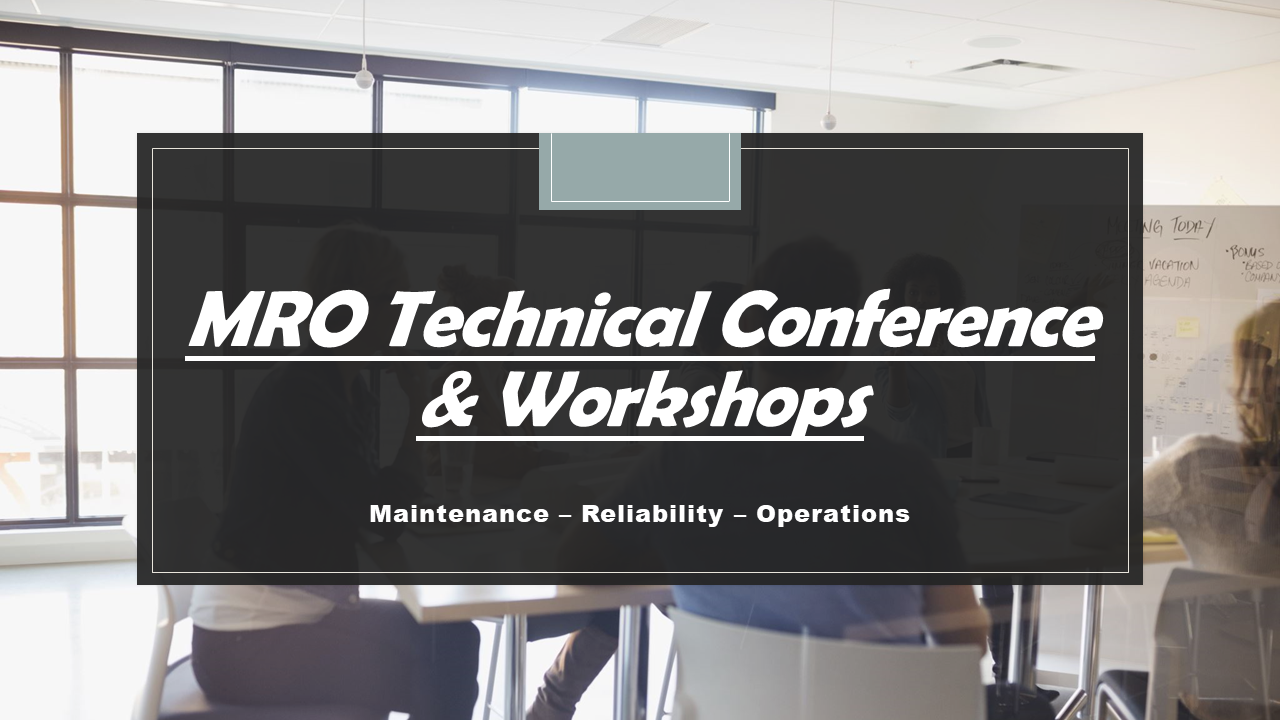
Combined Cycle Oil Filtration and Conditioning
PRESENTER
Michael Hilliard
Michael Long is a twenty-eight year employee and Vice President of The Hilliard Corporation. The majority of those years of service have been primarily in an engineering management role. Michael is currently an Engineering Product Manager, Manager of the divisional Research and Development (R&D) department, and the designated Technical Sales Lead for the organization. Michael holds a MS degree and BS degree in Organizational Management from Keuka College and an AS degree in Mathematics from Corning Community College. Michael is a co-inventor on US Patent #20140338293-A1.
SUMMARY
There are many challenges to keeping lubricating and hydraulic oils in peak condition due to the extreme conditions these fluids encounter. Static discharge, varnish formation, moisture contamination, TAN (Total Acid Number) and particulate contamination are just a few of the problems with oils that today’s power plant operators need to be well educated about in order to keep these problematic
conditions in check. We will discuss causal factors for these problems, the conditions to look for to identify them, the recommended type and frequency of fluid testing and the preventative measures or maintenance that can be performed to manage the risk of fluid problems causing costly unscheduled shut downs and outages.
We will take a closer look at the phenomenon of Static Discharge and discuss the conditions that cause it to occur. We will review the prevailing technologies available to prevent static discharge in lubricating applications and talk about the criteria for selecting the best prevention method. Ionic Exchange technology will also be a focus of this discussion as a prevention as well as remediation tool. The
multiple variations of this media type and the benefits and intended purpose of each will be illustrated. This presentation will review specific circumstances and case studies from the field to illustrate the prevention and remediation of these problematic fluid conditions.