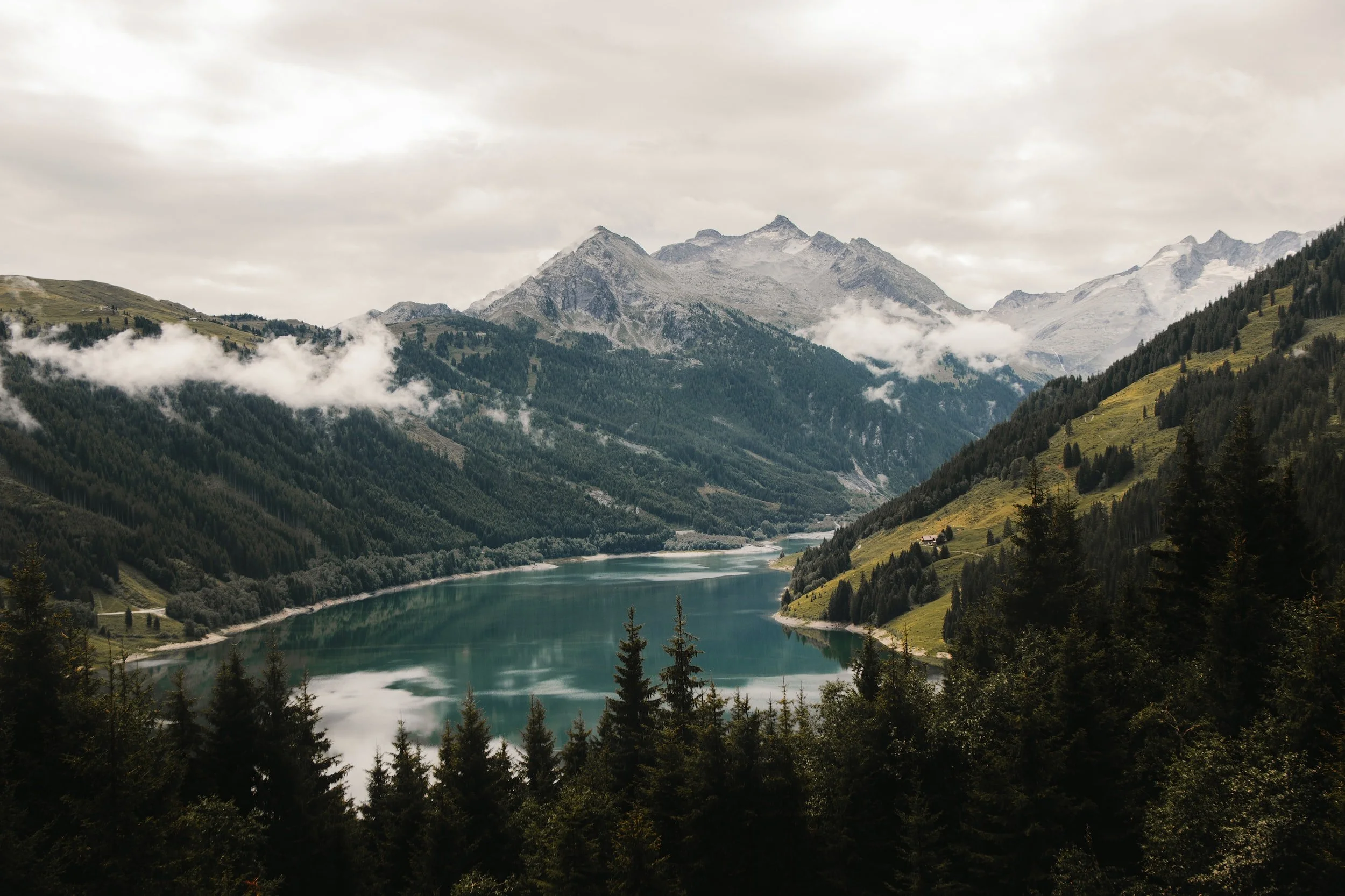
RATS MRO Conference
Presentation ARchive
2023 Presentations
2022 Presentations
2018 Presentations

Torsional Vibration Solutions
PRESENTERS
Bob Whitney
Bob is the Innvoations Director for Riverhawk Company based out of Whitesboro, New York.
Earl Boyd
Earl is the proprietor & president of Solutions 4ltd. His 45 years of experience in Industrial Power Transmission encompasses all aspects of business: planning, engineering, sales, marketing, senior management and directorships.
SUMMARY
Torsional vibration occurs often within shaft strings. In many cases the equipment runs well and tolerates the torsional vibration for long and dependable operation. On occasion torsional vibration developed within shafts that are not designed to tolerate it. Trouble can show up in a number of ways depending which part of operation is the most sensitive to torsional vibration.
Here is a short list of ways that torsional vibration can manifest:
Process variations such as sheet thickness in rolled products.
Fretting of joints leading to sloppy fits and wearing of components.
Lateral vibration where torque causes such movements, for example gear shafting.
Fatigue of shafting components which is notorious for sudden unexpected failures.
Structural overload, when torque values climb to levels that yield shaft material.
None of these results are desirable. When we become aware that a torsional problem exists we first need to learn a little bit about the nature of the vibration before a proper solution can be selected. Torsional vibration comes in a number of forms, each requiring a particular type of solution.
This presentation will discuss a number of torsional vibration types and attempts to describe their nature in a way that can be understood. It then discussed a series of solution approaches, describes how each addresses issues and provides some guidance on which solution types might work best for torsional vibration type.

Do we send this out, or rebuild it in our shop? Analysis of Today’s Maintenance Strategy
PRESENTER
Mark Tinis
Mark is the branch manager for Mi TechCan Services in Edmonton, a Division of Motion Canada. Mark has 24 years of experience with two different industry leaders in the heavy industrial and mechanical services sector.
SUMMARY
Machinery rebuild philosophies are constantly changing. It’s often hard to decide where crucial plant mechanical staff should be focusing their energy. “Should we be repairing this critical machine in our own shop, or sending out to a local service provider?” It’s a difficult question, but an important one. In this discussion, we will explore the advantages and disadvantages of all the options. We know the decision is never cut and dried and many factors contribute to your resulting verdict:
How critical is this machine to our operation?
How important is it that our staff understand every nut and bolt in it?
Do we have the in house knowledge to do the job right?
Who are the experts, and how do we leverage them to ensure a quality rebuild?
Do we have the right tools?
Is there other work in the plant that requires our people’s attention?
How do we reduce our overall cost of ownership?
We will explore and discuss all of these questions and more in this dynamic breakout session. Attendees are highly encouraged to actively participate in this session.

Motion Amplification: A New Way to Visualize Vibration
PRESENTERS
Mark van Bommel
Mark is an Owner/Director of Summit Services Group Ltd. a locally owned, certified aboriginal company. Mark has always been grounded in being hands with installation and maintenance for a wide variety of rotating and static equipment at many of their active works sites. With 12+ years of specializing in vibration analysis while working throughout western Canada and the USA, Mark is actively engaged in the Reliability world.
Janos Pattantyus
Janos is the RDI Technologies Sales Manager for the Canada world area. He puts his passion for vibration analysis and solving machinery problems to good use, initiating, training and supporting Canadian practitioners of asset health monitoring in Motion Amplification. Over his career, Janos worked as a permanent machinery protection system support specialist and as a condition monitoring consultant. Janos is a certified category IV vibration analyst with a master’s degree in mechanical engineering. He is a licensed Engineer in the province of Quebec.
SUMMARY
Motion Amplification enables you to quickly and easily see and analyze what is invisible to the naked eye and move to root-cause problem-solving. Software turns millions of pixels in today’s modern cameras into millions of individual data points that can be monitored, read, and analyzed.
This technology measures deflection, displacement, movement, and vibration not visible to the human eye. Camera technology is utilized in conjunction with software and processing algorithms to extract meaningful data. This technology turns every pixel in the camera’s view into a sensor capable of measuring vibration or motion with high levels of accuracy. The technology of motion amplification is presented. In particular, the application of this new tool to machine reliability is explored. One of the home-runs of reliability practitioners is to address the root cause of problems. Motion Amplification enables the user to see the big picture and generate actionable recommendations. A number of interesting case studies are used to illustrate this point.
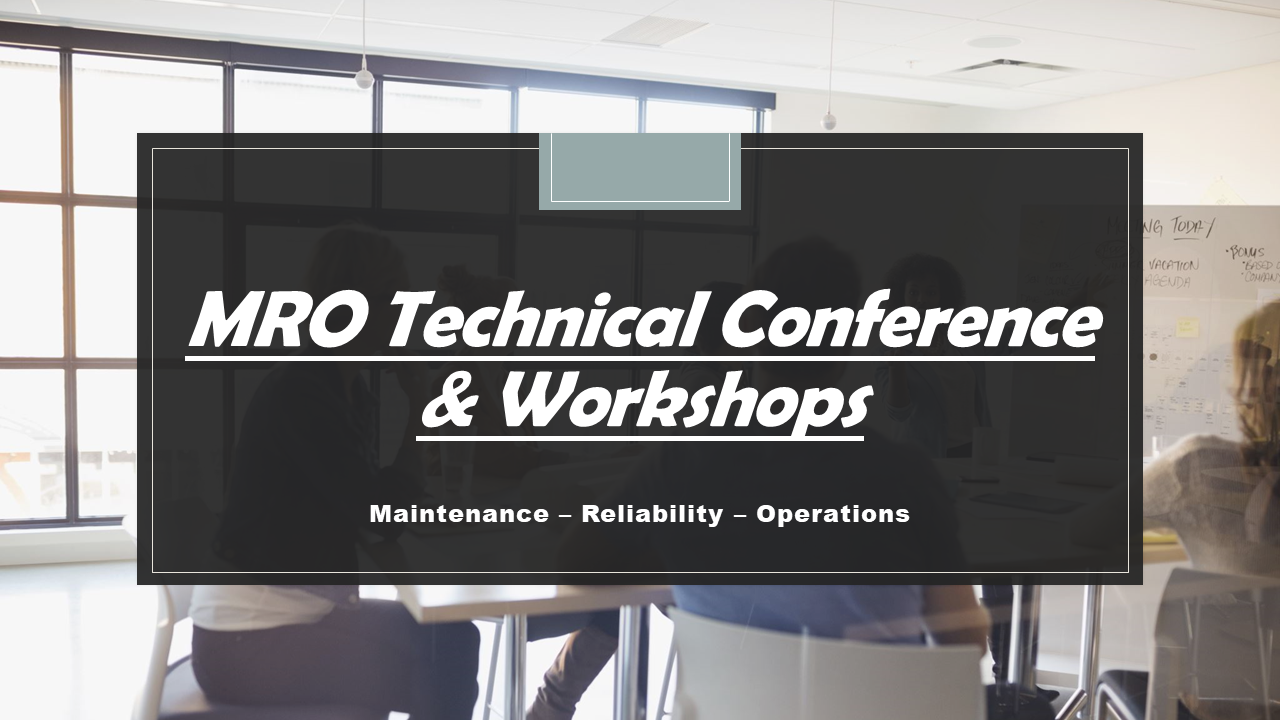
High Speed Geardrive Repairs – Industry Standards & Best Practices
presenter
Bernie L'Heureux
Bernie is the Regional Sales Manager at Standard Machine in Edmonton. He has over 20 years of experience in High and Low Speed Geardrives.
Summary
This presentation will highlight very specific and critical areas of high speed geardrive repair listed below:
Recording and review of operating conditions as time of decommissioning.
Driver/Gearbox/Driven Equipment - Considerations that affect repair.
Inspection and Failure Analysis - What levels are required?
Gear Repair v/s Gear Replacement.
Upgrades to API / AGMA standards - Why Instrument a Gearbox?
Assembly to OEM Specifications & Tooth contacts.
Testing - High Speed Drive Characteristics during testing.
Commissioning & Final Reports.